The Aluminum Wire Rod Breakdown Machine is a critical component in the production of high-quality aluminum wire. One of its most advanced features is the automatic correction control system for coiling tension, which plays a pivotal role in ensuring that the final product meets the necessary standards for wire consistency and quality. This system is designed to regulate the tension of the wire as it is drawn and wound onto spools, a crucial factor in maintaining uniformity throughout the manufacturing process. The technology behind it ensures that the wire does not suffer from issues like inconsistent diameters, breakages, or poor coil formation, which can otherwise affect both the material properties and the end-use performance of the wire.
At its core, the automatic tension control system works by continuously monitoring the tension applied to the wire during the drawing and coiling processes. This system is equipped with sensors that detect any fluctuations or changes in the wire’s tension as it moves through the machine. These sensors feed data to the machine's Programmable Logic Controller (PLC), which then makes real-time adjustments to the system to correct any inconsistencies. This means that if the tension becomes too high or too low, the PLC adjusts the feed rate or the motor speed to maintain the ideal tension. The result is a smooth, even process that eliminates the risk of wire breakage or uneven coiling, both of which can occur if tension control is inadequate.
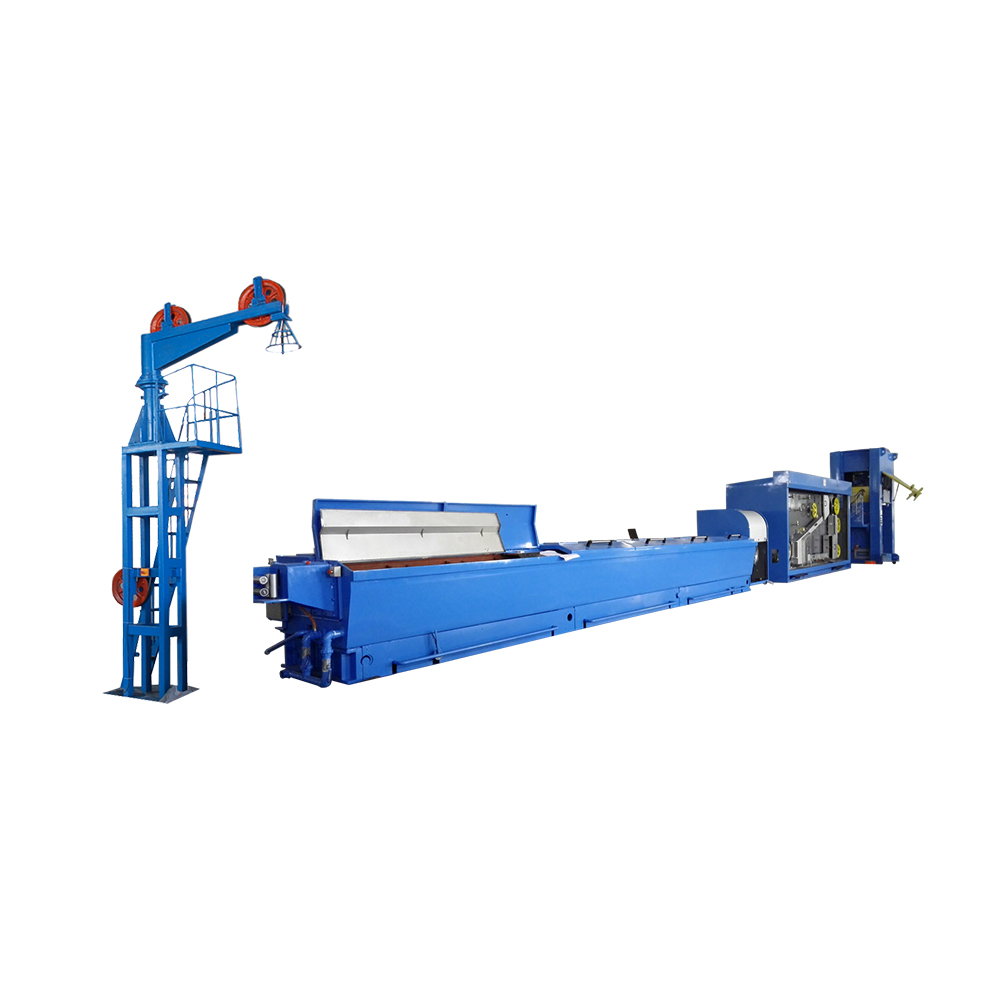
By using this automated system, the wire quality is significantly improved. Wire diameter consistency is one of the most crucial factors in determining wire performance. Even minor variations in diameter can affect the strength, flexibility, and conductivity of the aluminum wire, especially for applications in the electrical or construction industries. The automatic tension control system helps avoid such inconsistencies by providing a steady, regulated pull on the wire. As the wire is drawn from a thicker rod to thinner gauges, maintaining constant tension ensures that the wire retains its shape and uniformity throughout the entire length, which is essential for producing high-quality, reliable wire.
In addition to improving diameter consistency, the system also enhances the coiling process. As the wire is wound onto the spool, maintaining proper tension is critical to ensuring that the wire does not become tangled, compressed, or poorly wound. Poor coil formation can lead to storage issues, damage during transportation, or difficulties in future handling during the manufacturing process. The automatic correction system ensures that each coil is evenly wound with the right amount of tension, preventing these problems. This feature also reduces the need for manual adjustments, minimizing human error and increasing the overall efficiency of the production line.
The practical impact of the automatic correction control system goes beyond just improving the quality of the wire. It also contributes to efficiency and cost-effectiveness. Since the system adjusts the tension automatically, operators don’t have to make constant manual checks and corrections. This reduces downtime and maintenance needs, allowing for continuous, uninterrupted production. Additionally, the system helps reduce waste, as it prevents issues like wire breakage and defects that can lead to material losses. In turn, this not only enhances the quality of the final product but also optimizes the production process, resulting in cost savings for manufacturers.
With the integration of this advanced tension control system, the Aluminum Wire Rod Breakdown Machine provides a significant leap in wire production technology. The combination of precise tension management, automated adjustments, and real-time monitoring ensures that the wire’s final characteristics are consistent, reliable, and of the highest quality. Manufacturers can confidently rely on this feature to produce aluminum wire that meets stringent industry standards, while also improving operational efficiency and reducing overall production costs.
Contact Us