Copper wire drawing machines are essential in producing high-quality copper wires for various industrial applications, and the choice of machine configuration can significantly impact efficiency, quality, and production speed. Among the various options, horizontal-type wire drawing machines have garnered particular interest due to their unique design and operational advantages, especially compared to vertical models. With advanced features like precise speed control, energy-saving technology, and streamlined die changes, horizontal copper wire drawing machines provide high performance and cost-effective production, making them a preferred choice for many manufacturers.
One of the standout advantages of the horizontal configuration lies in its ability to handle continuous high-speed drawing with remarkable stability. Horizontal wire drawing machines are specifically designed to handle larger copper rods, beginning with diameters as thick as 8.0mm and drawing them down to ultra-fine diameters as low as 0.03mm. This design allows for a smooth, consistent drawing process where the wire experiences less vibration and tension fluctuations compared to vertical models. In a vertical setup, gravitational forces can sometimes lead to uneven tension distribution along the wire, especially during high-speed operations. The horizontal format, however, keeps the copper wire at a consistent angle and speed, minimizing disruptions and maintaining uniform tension. This advantage is particularly useful for manufacturers producing high-precision wires that must adhere to stringent diameter tolerances.
Another key feature of horizontal wire drawing machines is their integrated, user-friendly control system, typically equipped with PLC and HMI interfaces. These controls provide operators with easy, centralized management over the drawing speed, tension adjustments, and overall system diagnostics. In contrast, vertical machines often require additional adjustments to account for the changing tension and wire alignment due to the vertical pull, which can complicate the process and may even introduce slight inconsistencies in the wire thickness. The horizontal machines, on the other hand, allow operators to maintain a constant wire alignment throughout the drawing process, enabling smooth, uninterrupted operation. The PLC system also supports remote monitoring and automated alerts, enhancing the machine’s performance by allowing for quick adjustments as production demands change. This level of control helps reduce material waste, optimizes energy usage, and maintains product quality.
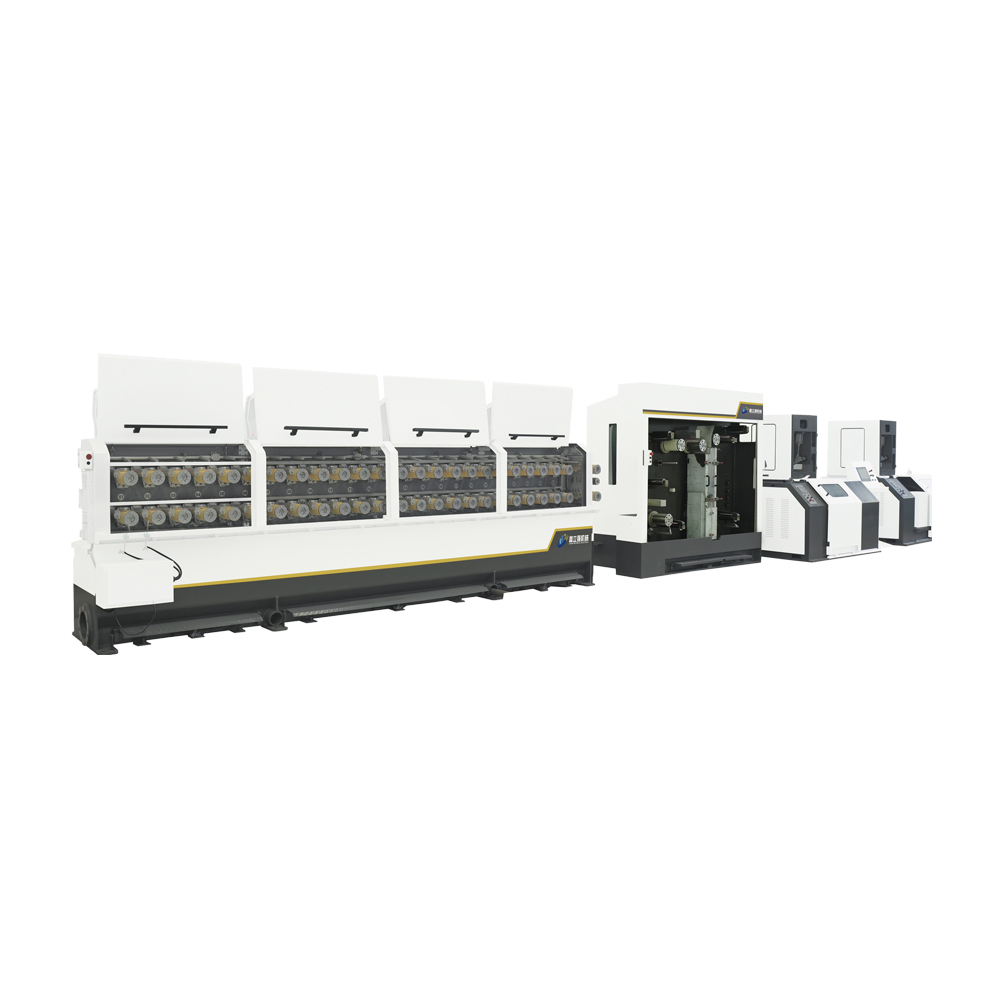
The energy efficiency of horizontal wire drawing machines is another critical benefit that resonates with manufacturers focused on operational cost reduction and sustainability. In horizontal setups, the machine's components—such as capstans, die assemblies, and spooling systems—are configured in a way that allows for minimal energy loss. By maintaining consistent wire tension and reducing the need for frequent adjustments, horizontal machines conserve energy over long production cycles, especially when drawing high volumes of copper wire in rapid succession. Additionally, some models incorporate advanced die-change mechanisms that allow for rapid adjustments without a complete production halt, thus saving both time and energy. This efficiency not only contributes to lower operational costs but also aligns with many manufacturers’ goals to reduce environmental impact by minimizing wasted energy and materials.
The versatility in output options, such as the choice between single spoolers, double spoolers, or drop coilers, also highlights the practical advantages of horizontal copper wire drawing machines. In many high-volume production settings, manufacturers need flexibility in how they handle and store finished wire. Horizontal machines accommodate multiple spooling configurations, allowing facilities to adapt quickly based on order requirements or specific project needs. This adaptability can be particularly valuable in production environments where copper wire diameters may vary, or where end-product packaging and handling requirements change frequently.
The horizontal-type configuration offers a balanced blend of stability, efficiency, and adaptability that is difficult to achieve with vertical models. This design is not only easier to operate but also reduces the learning curve for operators, allowing for efficient handling of different copper wire sizes. Given these benefits, it's no surprise that horizontal copper wire drawing machines continue to stand out in high-performance manufacturing settings, offering companies a reliable way to meet stringent quality standards while optimizing production costs and minimizing energy use. For industries where precision and productivity go hand in hand, the horizontal configuration is a clear choice that maximizes output quality without compromising operational efficiency.
Contact Us