In the manufacturing of high-performance brass wire, the ability to adapt to varying wire diameters is critical for meeting industrial demands. Brass Wire Drawing Machines excel in this domain by integrating cutting-edge engineering solutions that ensure precision, flexibility, and consistency across applications ranging from electrical components to EDM (Electrical Discharge Machining) wires. Here’s how these machines achieve unparalleled versatility in processing brass wire of different gauges.
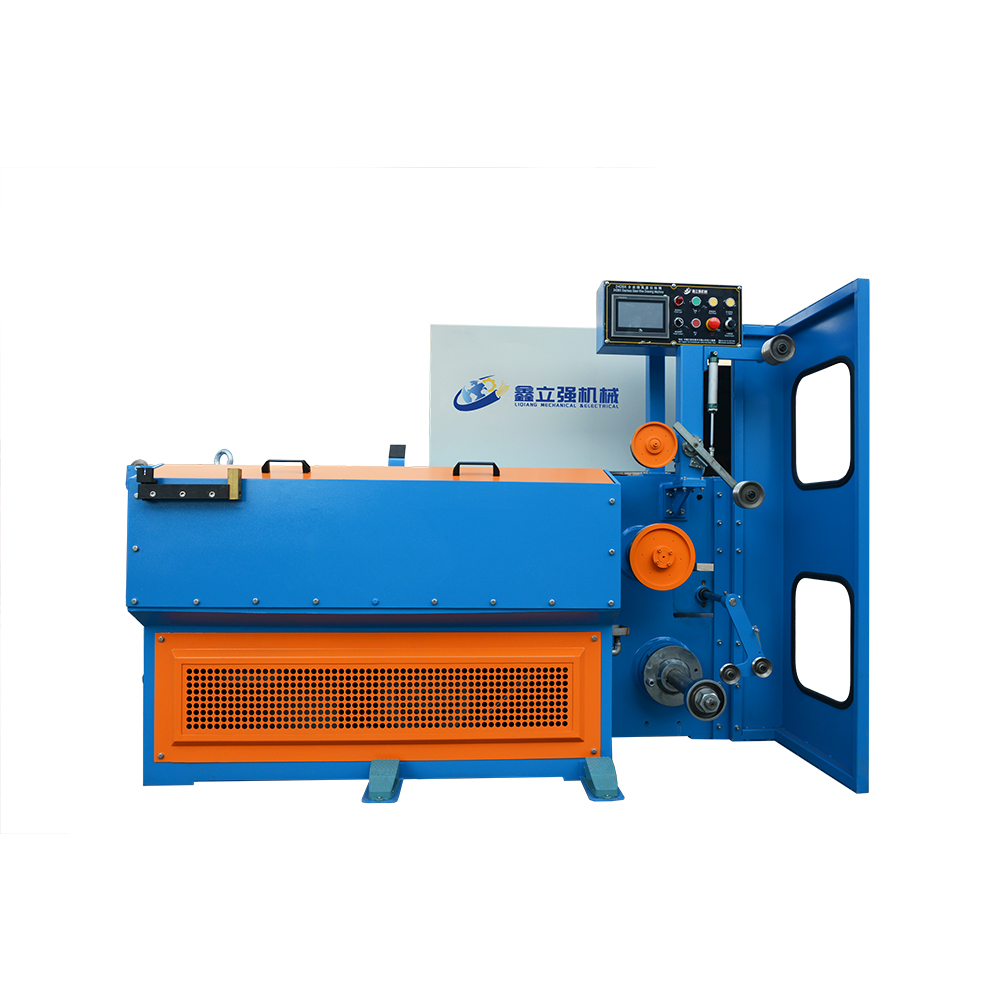
1. Adaptive Design for Multi-Gauge Processing
Modern brass wire drawing machines are engineered to handle wire diameters spanning 0.1–0.6mm, a range that caters to both ultra-fine and mid-sized industrial requirements. For instance, specialized configurations support 0.25–0.6mm wires for robust electrical conductors or 0.1–0.32mm filaments for precision EDM applications. This adaptability is achieved through modular die setups, such as 24-stage drawing systems, which systematically reduce wire diameter while maintaining structural integrity. By optimizing die alignment and tension control, these machines minimize material stress, ensuring uniform surface finish and dimensional accuracy even during extreme gauge transitions.
2. Intelligent Control Systems for Seamless Operations
The integration of Siemens PLC and HMI interfaces revolutionizes the brass wire drawing process. Operators can pre-program parameters for different wire sizes, automating speed adjustments, lubrication cycles, and tension calibration. Real-time monitoring via the HMI dashboard enables quick troubleshooting, while the automatic tension correction system dynamically adjusts coiling forces to prevent wire breakage or uneven winding. Such smart controls not only enhance production efficiency but also reduce downtime, making these machines ideal for high-volume, multi-specification manufacturing environments.
3. Durability and Maintenance Efficiency
Constructed with a cast iron monoblock frame, brass wire drawing machines prioritize rigidity and vibration resistance—key factors for maintaining precision over prolonged operations. The belt-driven transmission system further enhances reliability by minimizing mechanical wear and simplifying maintenance. Unlike traditional chain-driven systems, belt mechanisms reduce noise and energy consumption while allowing rapid die replacements or alignment corrections. Combined with modular components, this design ensures quick reconfiguration for different wire gauges, empowering manufacturers to switch production profiles without compromising throughput.
For industries requiring high-precision brass wire, these advanced drawing machines represent a transformative solution. By harmonizing robust engineering with intelligent automation, they address the complexities of multi-gauge production while delivering cost-effective scalability—a testament to innovation in metal processing technology.
Contact Us