In the fast-paced world of wire manufacturing, the Automatic Wire Take Up Machine is the unsung hero of efficiency, seamlessly coiling copper, steel, aluminum, and brass wires with precision. But even the most robust machinery requires proactive care to sustain peak performance. For industries relying on high-speed coiling, understanding how to optimize service life and manage replacement parts isn’t just a maintenance task—it’s a strategic imperative. Let’s dive into the nuts and bolts of keeping your wire take-up systems running smoothly for years.
Service Life Optimization: Beyond the Basics
The longevity of an Automatic Wire Take Up Machine hinges on predictive maintenance protocols tailored to its operational demands. For facilities running 24/7 production cycles, continuous monitoring of critical components like bearings, tensioners, and drive systems is non-negotiable. Advanced techniques such as vibration analysis and thermal imaging can detect early signs of wear, preventing catastrophic failures during high-speed coiling of abrasive materials like stainless steel. For instance, guide rollers subjected to constant friction from carbon steel wires may require specialized coatings or periodic realignment to avoid uneven wear.
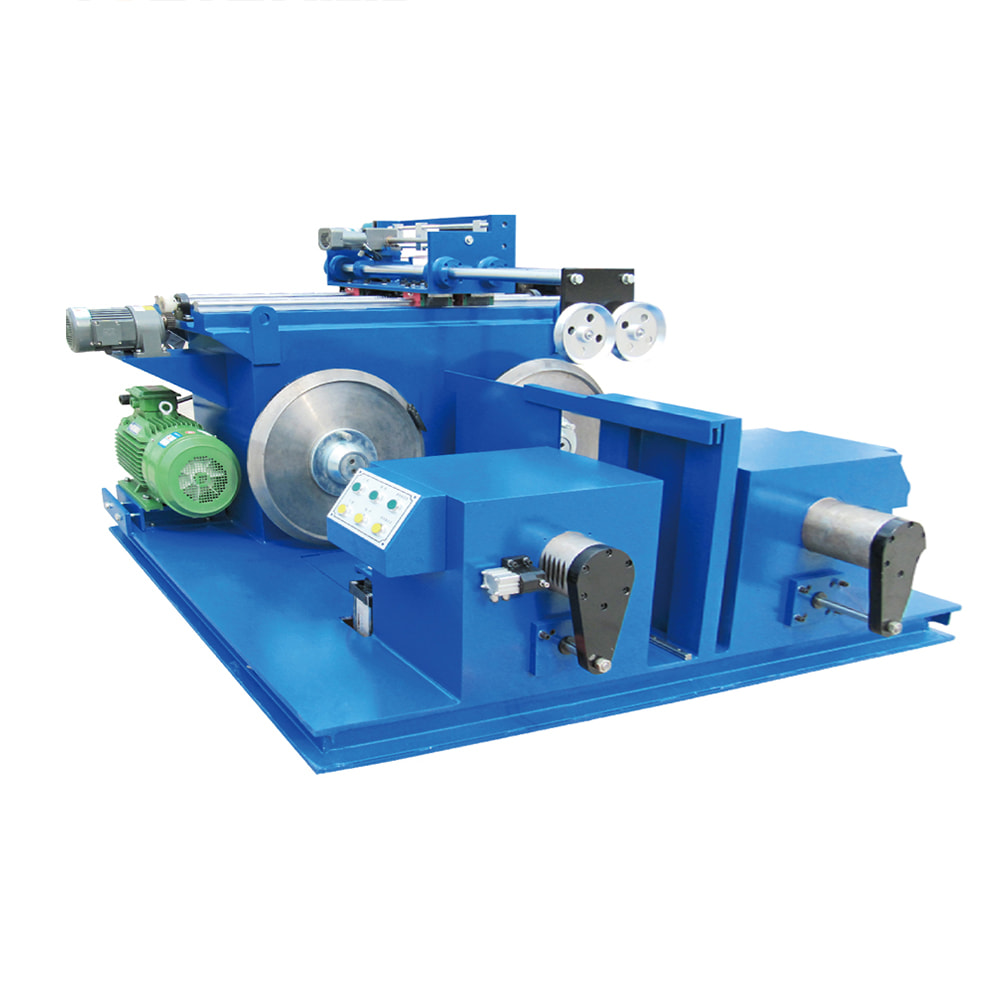
Equally vital is addressing material-specific challenges. Aluminum’s lightweight nature might seem gentle on machinery, but its softness can lead to residue buildup in spool holders, causing slippage. Similarly, high-tensile steel wires demand reinforced tension control systems to prevent micro-cracks in the machine’s framework. Implementing a maintenance schedule that accounts for these nuances—such as biweekly lubrication for high-contact parts or monthly inspections of alignment sensors—ensures the machine adapts to varying workloads without compromising precision.
Replacement Parts: Balancing Availability and Performance
When wear-prone components do reach their limit, the efficiency of your Automatic Wire Take Up Machine depends on seamless part replacement. One common concern is whether critical parts like belts, bearings, or tensioners are standardized or proprietary. Standardized components reduce downtime, as they’re often readily available from third-party suppliers. However, proprietary parts, while potentially costlier, are engineered to tighter tolerances, ensuring compatibility with the machine’s high-speed dynamics.
Lead times for replacements also play a pivotal role in operational planning. For example, a facility processing specialty brass wires might prioritize keeping spare guide rollers on-site to avoid halting production during unexpected failures. Manufacturers often provide tiered support packages: basic plans cover common wear parts, while premium tiers include expedited shipping for urgent needs. Proactive inventory management—paired with insights from the machine’s diagnostic systems—can slash downtime by up to 40%, according to industry benchmarks.
The Hidden ROI of Preventive Care
Investing in maintenance isn’t just about avoiding breakdowns; it’s about safeguarding your bottom line. A well-maintained Automatic Wire Take Up Machine consumes less energy per coiled kilometer, thanks to reduced friction and optimized motor performance. For instance, a servo motor operating under proper tension settings can lower power costs by 15–20% compared to an overworked unit. Additionally, extending the machine’s lifespan delays capital expenditure on new equipment, freeing up resources for innovation or market expansion.
Training operators to recognize early warning signs—unusual vibrations, inconsistent coiling patterns, or abnormal noise levels—further amplifies these benefits. Pairing hands-on workshops with digital tools like IoT-enabled dashboards allows teams to monitor metrics such as coil tension variance in real time, transforming reactive repairs into data-driven preventive strategies.
The Automatic Wire Take Up Machine is more than a piece of equipment—it’s the backbone of modern wire production. By prioritizing predictive maintenance, strategic parts management, and operator training, manufacturers can unlock unparalleled efficiency and durability. Whether coiling delicate aluminum strands or rugged steel cables, a proactive approach ensures your machine remains a reliable partner in meeting the demands of tomorrow’s industrial challenges. Remember, the true measure of a machine isn’t just its speed—it’s how well it endures.
Contact Us