A steel wire drawing machine is an essential piece of equipment in the manufacturing industry, used to reduce the diameter of steel wire while simultaneously increasing its length, strength, and flexibility. The process begins with the preparation of the wire rod, which is first cleaned to remove any surface impurities that could interfere with the drawing process. This is crucial because any contamination can damage the delicate dies or result in a substandard final product.
Once cleaned, the wire rod is fed into a pointing machine, which tapers the end of the rod. This pointed end is then threaded through the first drawing die, which is the heart of the wire drawing machine. Drawing dies are made from exceptionally hard materials such as tungsten carbide or diamond, chosen for their durability and ability to withstand the high stresses involved in the drawing process. These dies have precisely machined holes that shape the wire as it is drawn through them.
The wire drawing process involves pulling the tapered end of the wire through the die by a rotating capstan, a drum powered by an electric motor. The capstan ensures a consistent drawing speed, which is critical for maintaining the quality of the drawn wire. The wire is drawn through the die, reducing its diameter. This reduction increases the wire's length and enhances its tensile strength. Depending on the required final diameter, the wire might pass through multiple dies, each progressively smaller, in a multi-stage process.
A vital component of the wire drawing machine is its lubrication system, which applies lubricants to both the wire and the die to reduce friction and prevent wear and tear on the die. Proper lubrication is essential for achieving smooth and efficient drawing operations and for extending the life of the dies. Additionally, a cooling system is integrated to keep both the wire and the drawing dies at an optimal temperature, preventing overheating that could compromise the material properties.
Control over the drawing process is managed by advanced control systems, typically comprising a Programmable Logic Controller (PLC) and a Human-Machine Interface (HMI). The PLC automates the process, ensuring precise control over variables like speed and tension, which are critical for producing wire of uniform diameter and high quality. The HMI provides a user-friendly interface for operators to monitor and adjust the process, making the operation of the machine more intuitive and efficient.
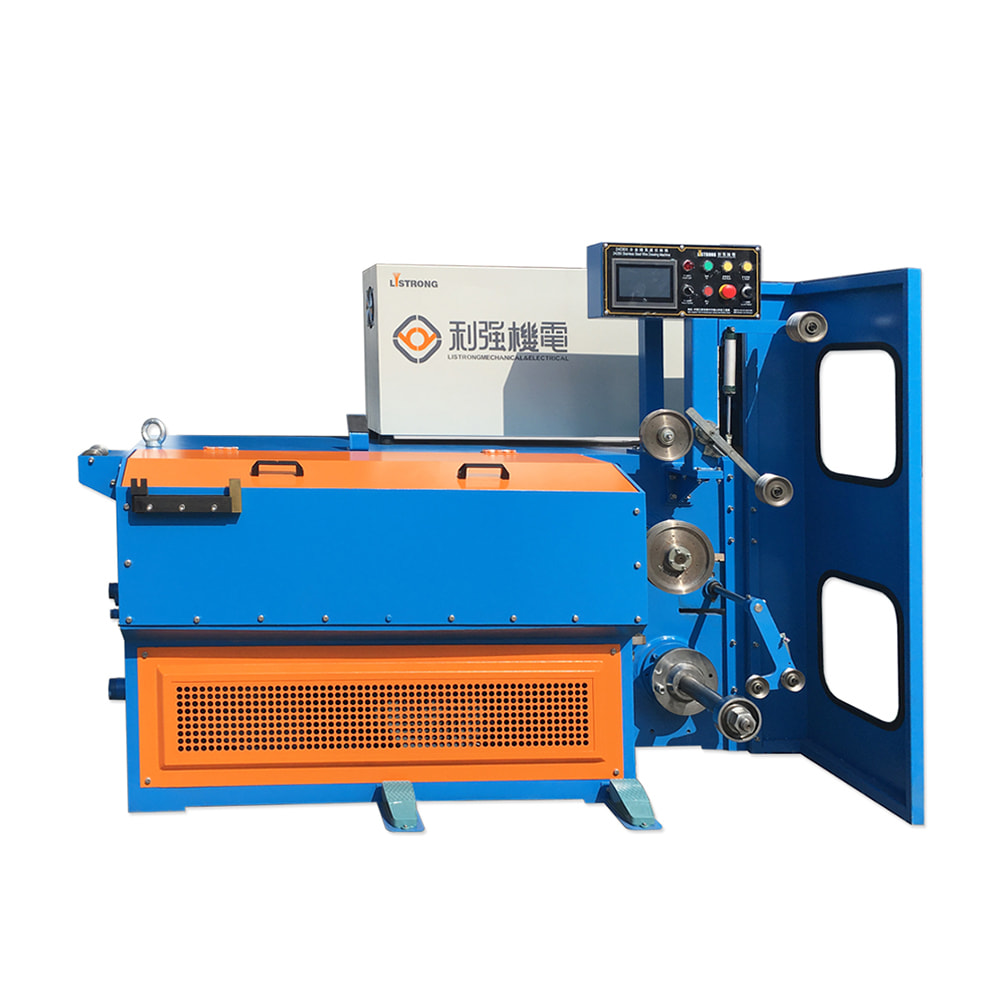
After the drawing process, the wire might undergo annealing, a heat treatment procedure to relieve internal stresses and enhance ductility. This is especially important if the wire is to be further drawn or if specific mechanical properties are required for its intended application. The drawn wire is then collected by a take-up mechanism, which can be a single take-up, double take-up, or a drop coiler, depending on the configuration of the machine. This ensures that the wire is neatly wound onto spools or coils, ready for further processing or shipment.
The advantages of steel wire drawing machines are manifold. They offer high-speed operation and automation, significantly boosting production efficiency. The ability to draw wires of various diameters makes these machines versatile, catering to diverse industry needs, from automotive and construction to consumer goods and biomedical applications. The integration of high-quality components, such as durable capstans and precision-engineered dies, ensures long-term performance and reduces maintenance costs. Moreover, the advanced control systems enhance the ease of operation, allowing even less experienced personnel to manage the drawing process effectively.
In summary, a steel wire drawing machine works by pulling wire through a series of progressively smaller dies to reduce its diameter and increase its length. Key components involved include the payoff, pointing machine, drawing dies, drawing capstan, lubrication system, take-up mechanism, control system, and cooling system, with optional annealing furnaces for intermediate heat treatment. These components work in concert to ensure efficient, precise, and continuous wire drawing operations, making these machines indispensable in modern manufacturing.
Contact Us