In recent years, technological advancements have revolutionized copper wire drawing machines, enhancing their efficiency, precision, and overall performance in industrial applications. Traditionally vital in the production of copper wires used extensively across industries like electronics, telecommunications, and power distribution, these machines have undergone significant transformations driven by innovations in automation, materials science, and digitalization.
One of the most notable advancements lies in the realm of automation. Modern copper wire drawing machines are equipped with sophisticated PLC (Programmable Logic Controller) systems and intuitive HMI (Human-Machine Interface) panels. These advancements enable seamless control over the drawing process, allowing operators to monitor and adjust parameters such as speed, tension, and diameter with unprecedented precision. This level of automation not only enhances operational efficiency but also minimizes human error, ensuring consistent quality in the final wire products.
Technological improvements have also focused on enhancing the precision and accuracy of the wire drawing process. Advanced sensors and actuators now enable precise control over drawing forces and speeds, crucial for achieving uniform wire diameters across production batches. This capability is especially critical as industries demand increasingly finer gauges of copper wire for applications ranging from intricate electronics to high-speed data transmission cables.
Materials science has played a pivotal role in extending the lifespan and durability of copper wire drawing machines. Components such as dies and capstans are now crafted from advanced materials that offer superior wear resistance, reducing maintenance downtime and operational costs. These enhancements not only ensure prolonged machine reliability but also support sustained high-performance output over extended production cycles.
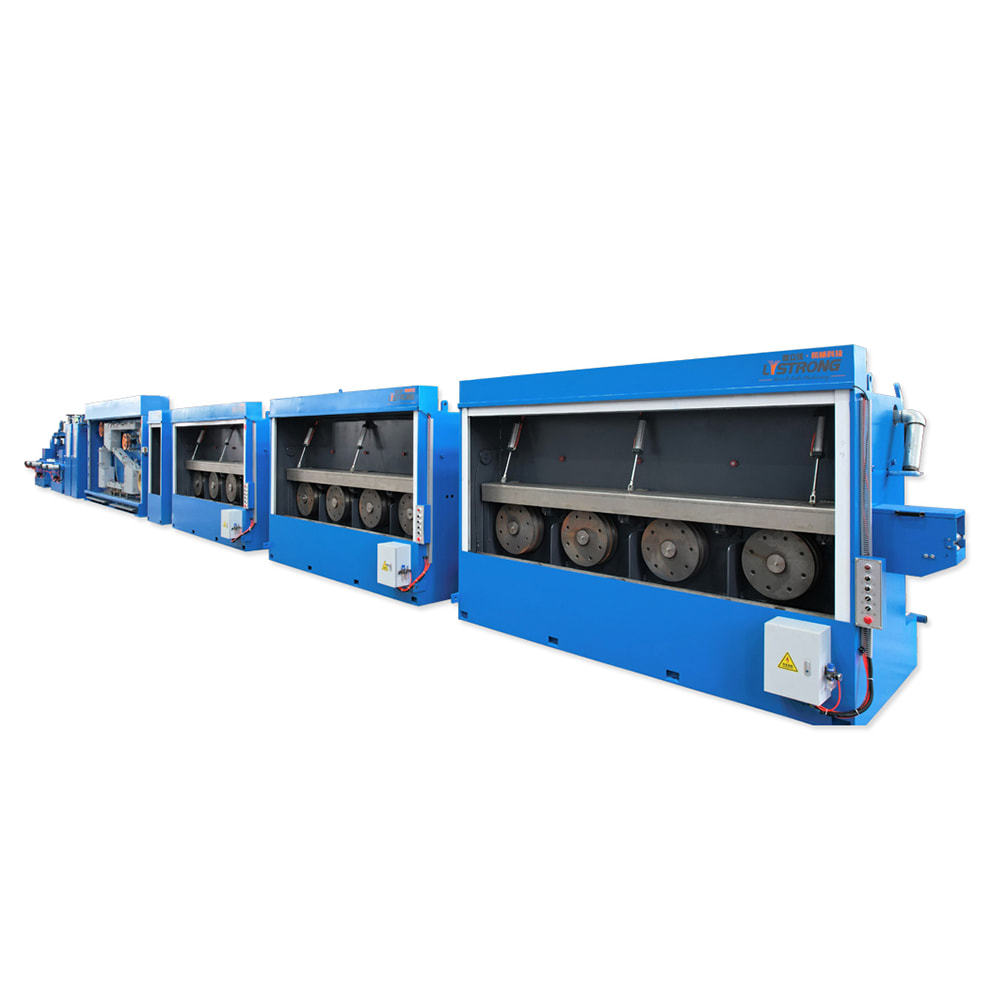
Energy efficiency has also seen significant strides in recent copper wire drawing machine designs. The integration of energy-efficient motors and optimized mechanical systems has minimized power consumption without compromising on operational output. This not only translates into cost savings for manufacturers but also aligns with global sustainability initiatives by reducing the machines' carbon footprint.
Furthermore, advancements in rapid die-change systems have transformed operational flexibility. Modern machines can swiftly switch between different wire diameters and spooling configurations, accommodating diverse production requirements with minimal downtime. This agility is crucial in today's dynamic manufacturing environments where responsiveness and adaptability are key to maintaining competitive edge.
The evolution of copper wire drawing machines through technological advancements has ushered in an era of heightened efficiency, precision, and sustainability in industrial wire production. From enhanced automation and digital control systems to improved materials and energy efficiency measures, these advancements have not only elevated the capabilities of these machines but also expanded their application potential across a spectrum of industries. As demands for finer wires and higher production volumes continue to grow, these technological innovations ensure that copper wire drawing machines remain indispensable tools in modern manufacturing landscapes, driving innovation and reliability in global supply chains.
Contact Us