Copper wire drawing machines play a vital role in modern manufacturing, producing wires of various diameters essential for industries ranging from electronics to construction. These machines are engineered to handle the drawing of copper rods, reducing their size through dies, often down to diameters as small as 0.03mm. As they perform this critical task, several factors contribute to the efficiency and quality of the final product, one of which is lubrication. Lubrication plays an essential role in copper wire drawing, ensuring that the machine operates smoothly and that the wire is drawn without defects.
Lubrication in copper wire drawing serves several key functions. First and foremost, it reduces friction between the copper rod and the drawing die. As the copper wire passes through successive dies, it experiences significant tensile forces, and the resulting friction can lead to high temperatures. Without proper lubrication, this friction could damage both the wire and the die, leading to premature wear, wire breakage, or surface imperfections on the wire. A well-lubricated drawing process ensures that these issues are minimized, leading to smoother operations and higher-quality wire production. Lubricants also help in heat dissipation. As friction generates heat, particularly when drawing smaller wire diameters at high speeds, excessive temperatures can soften or deform the copper wire. Effective lubrication prevents overheating, maintaining the integrity of the wire as it is drawn.
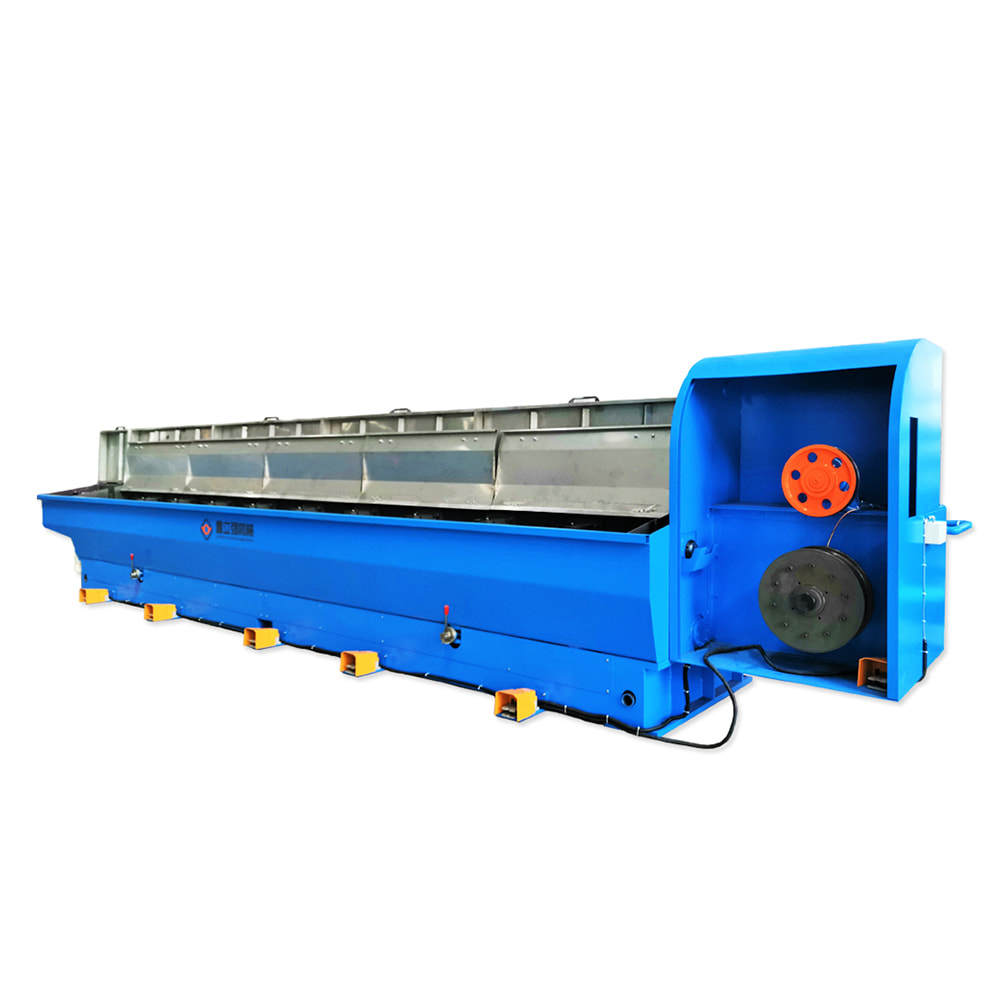
Managing lubrication in modern copper wire drawing machines is a sophisticated process. Many machines, especially those equipped with PLC (Programmable Logic Controller) and HMI (Human-Machine Interface), feature automated lubrication systems that monitor and control the amount of lubricant applied during the drawing process. This ensures the optimal balance between reducing friction and maintaining the necessary drawing forces to shape the wire properly. High-performance machines often have a closed-loop lubrication system, where the lubricant is recycled, filtered, and cooled before being reintroduced into the system. This not only improves the machine's efficiency but also contributes to energy savings and sustainability by reducing waste and limiting the need for frequent lubricant replacement.
In addition to automated lubrication systems, the type of lubricant used is carefully selected based on the specific requirements of the wire drawing process. For instance, water-based lubricants are commonly used when drawing finer wires, as they provide excellent cooling properties while maintaining low viscosity to reduce drag. Oil-based lubricants, on the other hand, may be used for thicker wires that generate more heat, as they provide superior film strength and protection against wear. Advanced machines offer the flexibility to switch between different types of lubricants depending on the size of the wire being drawn, further enhancing the machine’s versatility and adaptability.
lubrication is indispensable in copper wire drawing, ensuring the smooth operation of the machinery, protecting the copper wire from damage, and prolonging the lifespan of key components like dies and capstans. As copper wire drawing machines continue to evolve with advancements in automation and precision engineering, the management of lubrication remains a critical aspect of maximizing efficiency, reducing energy consumption, and producing high-quality copper wire. By integrating sophisticated control systems and employing the right lubricants for specific wire diameters, these machines not only enhance production but also contribute to the commercial value of copper wire manufacturing.
Contact Us