Maintaining and servicing a wire cable bunching machine is essential to ensure its longevity and efficient operation, particularly in environments where it plays a critical role in producing high-quality wire products. These machines are designed for twisting multi-strand bare copper, tinned wires, and other materials, and are integral to the wire manufacturing process. Proper care and maintenance not only extend the life of the machine but also prevent operational downtime, reduce repair costs, and maintain consistent production quality.
To maintain a wire cable bunching machine, it is important to follow a structured routine that includes regular inspections, cleaning, lubrication, and timely replacement of worn-out parts. The electrical components, which are often imported and highly sensitive, should be regularly checked for any signs of wear, loose connections, or overheating. Since these components are the heart of the machine's operation, ensuring they function optimally is critical. Operators should keep a close eye on the touchscreen controls and other interface systems, ensuring they are responsive and free from dust or grime, as this can affect the machine's performance over time.
One of the key areas to monitor is the twisting mechanism. The machine operates at high speeds to twist wire strands, and the mechanical parts involved in this process are subject to wear and tear. Regular lubrication of moving parts—including gears, bearings, and rotating shafts—helps reduce friction, minimize heat buildup, and prevent premature failure. It’s essential to use the manufacturer-recommended lubricants to avoid compatibility issues that could damage the components. Moreover, any abnormal noise, vibration, or heat should be addressed immediately to prevent more serious issues from developing.
Cleaning the machine regularly is also a fundamental part of maintenance. Since wire production can generate dust, metal shavings, or residues, these materials can accumulate in and around critical areas such as the twisting chamber, wire guides, and electrical systems. A clean machine is less likely to suffer from operational issues such as clogging, misalignment, or electrical faults. Operators should use compressed air to blow out any accumulated debris, paying special attention to the ventilation systems to prevent overheating, which could damage both mechanical and electronic parts.
Another important aspect of maintenance is preventive inspection. Regularly inspecting the machine for signs of wear, especially on high-load areas such as belts, pulleys, and drive systems, can help identify problems before they result in breakdowns. If a part appears worn or damaged, it should be replaced immediately with genuine parts to ensure compatibility and performance. Preventive inspection also includes checking for proper alignment of the wire strands during twisting, as any misalignment could lead to inconsistent product quality and additional stress on the machine.
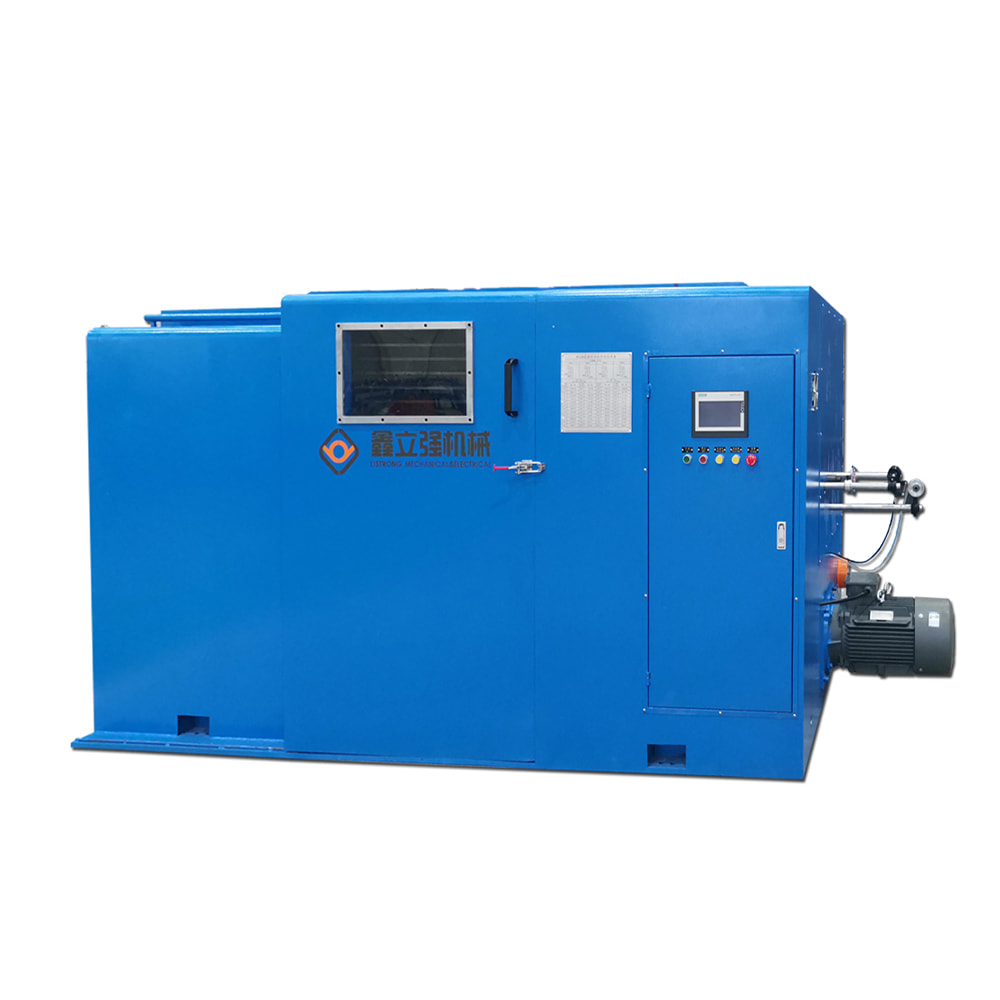
It is also crucial to train machine operators on proper handling and basic troubleshooting techniques. Understanding how to operate the machine within its recommended parameters prevents overloading or misuse, both of which can cause premature wear. Operators should be able to detect minor issues such as unusual noises or inconsistencies in the twisting process, allowing them to make adjustments before the problem escalates. Software updates and firmware upgrades are another factor to consider, as manufacturers often release improvements that enhance the machine's efficiency and safety features.
Moreover, regular calibration of the machine’s settings is essential to maintain accuracy in wire twisting, particularly when working with different wire sizes. Calibration ensures that the machine operates at optimal tension, speed, and pressure, minimizing stress on both the machine and the product. As many wire cable bunching machines are equipped with advanced control systems, these should be checked regularly to ensure all parameters are correctly set and functioning as intended.
Finally, maintaining a detailed service log is critical for tracking maintenance activities, part replacements, and any issues that arise over time. This documentation allows operators and technicians to identify patterns or recurring issues, which can guide future preventive measures. A well-maintained machine not only functions more efficiently but also ensures higher productivity, lower operational costs, and improved product quality, making it a valuable asset for any wire manufacturing operation. In conclusion, proactive maintenance, thorough cleaning, regular inspection, and proper operator training form the backbone of effective servicing for wire cable bunching machines, ensuring their long-term efficiency and reliability.
Contact Us