Rod Breakdown Machines (RBMs) can be highly automated, and control technology plays a crucial role in ensuring precision, efficiency, and safety in the wire drawing process. Here are key aspects of automation and control technology in
Rod Breakdown Machines:
Automated Tension Control:
RBMs often feature automated tension control systems that adjust the pulling force applied to the wire during the drawing process. This ensures consistent wire quality and minimizes the risk of breakage.
Speed Control and Synchronization:
Automation allows for precise control of the machine's speed, ensuring synchronization between different components. This is essential for maintaining uniform wire diameter and preventing inconsistencies.
Die Changeover Automation:
Some RBMs are equipped with automated die changeover systems, enabling a quick and seamless transition between different drawing stages. This reduces downtime and increases overall productivity.
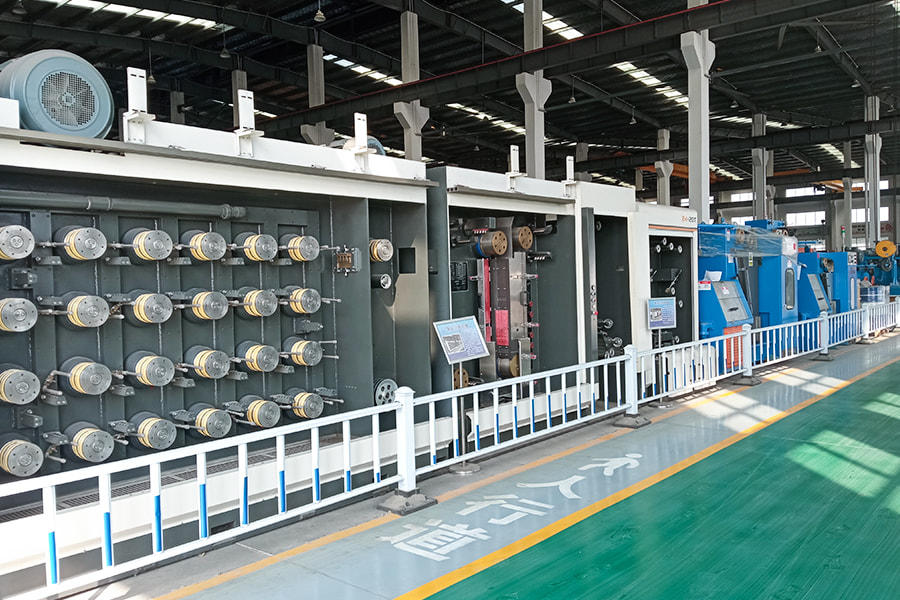
Process Monitoring and Control:
Automation systems continuously monitor various parameters such as wire diameter, temperature, tension, and speed. Control algorithms adjust these parameters in real-time to maintain optimal processing conditions and product quality.
Feedback Systems:
Sensors and feedback systems provide real-time data on the wire drawing process. This information is used to make automatic adjustments to the machine parameters, ensuring that the final product meets specified standards.
Quality Control Systems:
Automated quality control systems may include cameras, lasers, or other sensors that inspect the wire for defects, diameter variations, or surface imperfections. Automatic rejection mechanisms may be integrated to remove substandard products from the production line.
Energy Management:
Automation can optimize energy consumption by controlling the operation of motors, heaters, and cooling systems based on demand. This contributes to energy efficiency and cost savings.
Maintenance Diagnostics:
Automated systems can monitor the condition of machine components and predict potential issues. Predictive maintenance alerts operators to perform maintenance tasks before a breakdown occurs, minimizing unplanned downtime.
Human-Machine Interface (HMI):
RBMs often feature user-friendly interfaces that allow operators to monitor and control the machine. HMIs provide access to real-time data, historical records, and diagnostic information.
Integration with Production Lines:
Automation facilitates seamless integration with other machines in a wire manufacturing production line. Communication protocols and interfaces enable RBMs to work in coordination with upstream and downstream equipment.
Safety Systems:
Automated safety features, such as emergency stop functions and interlocks, enhance the overall safety of the machine. These systems can automatically shut down the machine in the event of a malfunction or unsafe condition.
Contact Us