Maintaining the consistency of wire tension and alignment during the operation of a
multi-wire machine involves a combination of proper setup, regular maintenance, and real-time monitoring. Here's a step-by-step guide to help you achieve and sustain consistent wire tension and alignment:
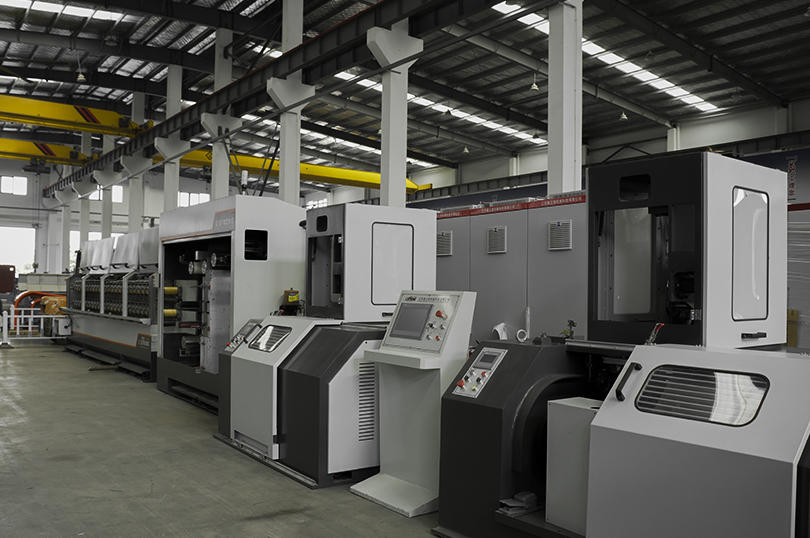
Machine Calibration:
Ensure that the multi-wire machine is regularly calibrated according to the specifications of the materials being processed. Calibration should include setting the appropriate tension levels for the wires.
Quality Wire Selection:
Use high-quality wires that have consistent diameter and material properties. Variations in wire quality can lead to differences in tension and alignment.
Tensioning System Inspection:
Regularly inspect the wire tensioning system for wear, damage, or malfunctions. Replace or repair any components that show signs of degradation.
Regular Maintenance Schedule:
Establish a routine maintenance schedule for the entire machine, focusing on key components such as tensioning systems, wire guides, and alignment mechanisms. Regular maintenance helps prevent issues and ensures consistent performance.
Real-Time Monitoring Systems:
Install sensors along the wire path to monitor tension levels in real-time. Connect these sensors to the machine's control system to enable continuous monitoring and adjustments during operation.
Automatic Tension Control:
Consider using a tensioning system with automatic adjustment capabilities. This feature allows the machine to adapt to changes in material properties or cutting conditions without manual intervention.
Alignment Mechanism Inspection:
Regularly inspect and maintain the alignment mechanisms of the machine. Misalignment can lead to uneven tension and affect cutting precision.
Wire Path Inspection:
Ensure that the wire path is free from obstructions and that wires are correctly threaded through guides and tensioning systems. Any deviations can impact tension and alignment.
Material Compatibility Checks:
Confirm that the machine settings are appropriate for the specific material being processed. Different materials may require adjustments in tension and alignment settings.
Operator Training:
Provide comprehensive training for
multi-wire machine operators. Operators should be familiar with the importance of maintaining wire tension and alignment and should know how to troubleshoot and make adjustments.
Emergency Stop Procedures:
Implement emergency stop procedures that allow operators to halt the machine immediately if tension or alignment issues arise. This prevents potential damage to the machine and ensures operator safety.
Synchronized Control System:
Ensure that the control system can synchronize the movements of multiple wires. Synchronized control is essential for maintaining consistent tension and alignment, especially during complex cutting operations.
Feedback and Reporting:
Establish a system for operators to provide feedback on any anomalies in wire tension or alignment. This information can be valuable for identifying recurring issues and implementing improvements.
Collaboration with Suppliers:
Work closely with wire suppliers to ensure consistent quality. Clear communication with suppliers can help address any issues related to wire quality promptly.
Documentation:
Maintain documentation for procedures related to setting up, calibrating, and adjusting wire tension and alignment. This documentation ensures consistency and serves as a reference for operators.
Contact Us