The good news is that many high-quality aluminum wire rod breakdown machines, especially those with advanced PLC and HMI controls, are designed to be flexible and versatile, making them suitable for a wide range of materials. However, adapting a machine to process different metals involves understanding the key adjustments needed to maintain efficiency and performance while avoiding costly damage to the equipment.
For starters, the machine’s drawing capabilities are closely linked to the physical properties of the material being processed. Aluminum is known for its relatively low tensile strength compared to other metals, so the machine’s design and motor specifications are optimized for this. When switching to other metals, such as copper, brass, or stainless steel, a few adjustments are necessary. The most important of these adjustments is the drawing speed and tension control. Different metals have varying degrees of ductility, and this will influence how the wire behaves during the drawing process. For harder metals, you may need to reduce the drawing speed and increase the tension slightly to avoid wire breakage or surface defects.
Additionally, the die setup will likely need to be reconfigured. Each metal has unique characteristics, such as hardness, malleability, and thermal conductivity, which influence the size and type of dies used in the breakdown process. For example, when processing harder metals like stainless steel, dies made from stronger, more wear-resistant materials are recommended to maintain efficiency and prevent excessive wear. These adjustments, while relatively straightforward, do require careful monitoring, and machine operators will need to have a clear understanding of the properties of each metal.
Another consideration is the machine's drive and transmission system. Aluminum’s lower melting point and softer nature make it easier to process, but when you switch to materials like copper, which are denser and more heat-resistant, the machine’s motor and drive mechanisms must be capable of handling the additional torque and resistance. While many modern wire rod breakdown machines are equipped with variable-speed motors and advanced tension controls, these systems may need to be recalibrated to ensure optimal performance when processing tougher materials.
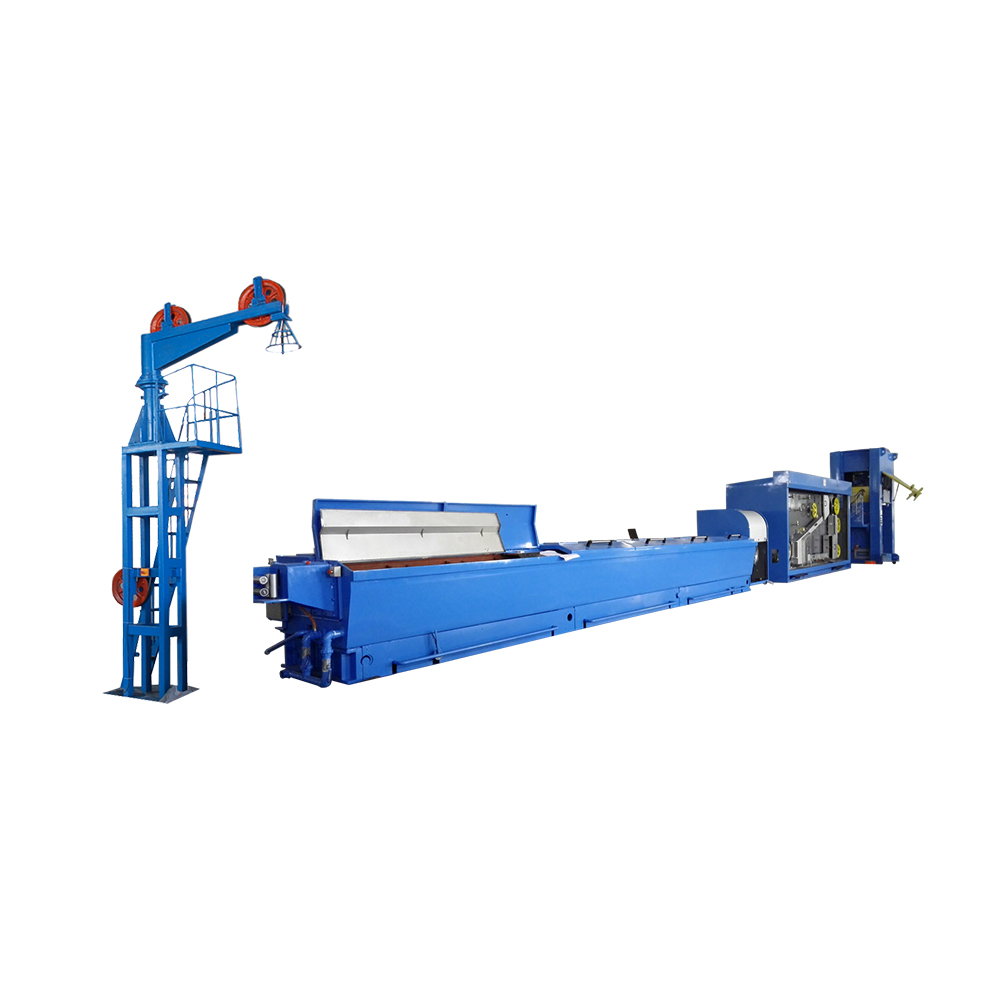
In terms of coiling, the machine’s spoolers and coiling systems must also be adjusted to handle the different weight and tension characteristics of the wire. Harder metals will require more precise tension control to ensure the wire is wound properly and doesn’t suffer from issues like excessive stress or damage. Additionally, depending on the metal, the coil's weight and diameter may need to be adjusted to accommodate the material’s density and strength.
While the machine is certainly adaptable to handle a variety of alloys, it’s crucial to remember that each metal comes with its own set of challenges. Therefore, manufacturers should consult with the equipment provider to ensure the machine is properly configured for the specific metal being processed. Some manufacturers offer customization packages or specific modifications that will optimize the machine for a broader range of materials. Ultimately, this flexibility in metal handling ensures that your production line can stay versatile and efficient, saving both time and costs while expanding your manufacturing capabilities.
While an aluminum wire rod breakdown machine is designed primarily for aluminum, it can be adjusted to handle other metals and alloys with a few key modifications. These include changes to the die setup, motor speed, tension controls, and coiling systems. With these adjustments, the machine can continue to perform at high efficiency, processing a variety of materials to meet the demands of different industries.
Contact Us