The longevity and smooth performance of the machine depend heavily on a solid maintenance schedule and easy access to high-quality replacement parts. Whether you're running the machine in a high-output environment or using it for more specialized applications, proactive maintenance is essential to minimize downtime, extend the lifespan of key components, and reduce unexpected repair costs.
A well-defined maintenance schedule is the foundation of keeping your steel wire drawing machine running smoothly. Generally, the routine upkeep should be carried out on a weekly, monthly, and annual basis. On a weekly level, operators should perform basic checks such as inspecting the wire drawing process for any irregularities, cleaning the machine to prevent dust buildup that could affect the drawing process, and verifying that the PLC and HMI systems are functioning properly. These systems are crucial for controlling the drawing speed, wire tension, and overall machine behavior, so ensuring they are calibrated correctly is key to maintaining consistency in wire production.
Monthly maintenance tasks should involve a more thorough inspection of the mechanical parts, particularly the capstan, which plays a crucial role in wire drawing. Given its critical function, the capstan should be checked for wear and tear to avoid any risk of failure. Regular greasing and lubrication of moving parts, including bearings, pulleys, and the take-up machine, will ensure smooth operation. It’s also advisable to perform checks on the wire guide system, ensuring that alignment remains perfect to avoid creating deformed or uneven wires.
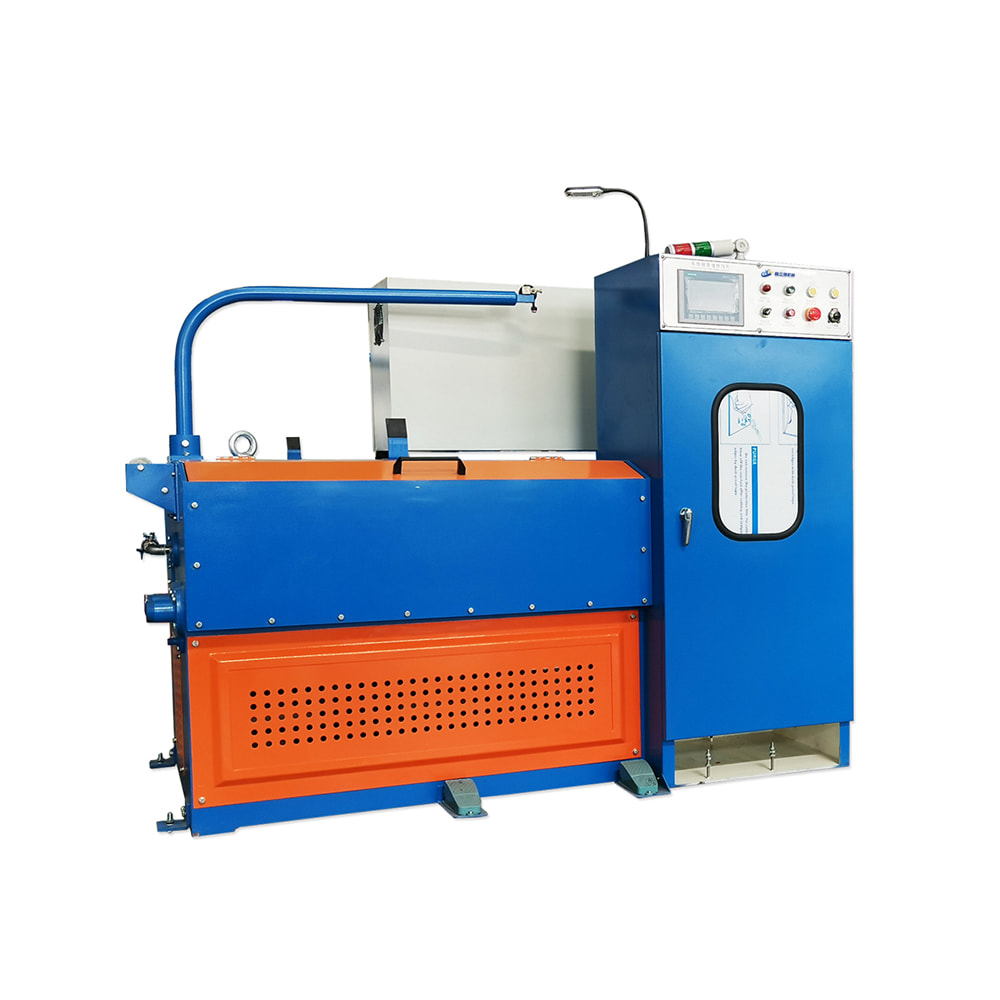
Annually, the machine should undergo a comprehensive inspection to replace any worn-out parts and check for any signs of excessive wear that could lead to future malfunctions. This is the time to replace any parts that are reaching the end of their service life, such as the capstan, motor components, or drive system. During this time, the overall condition of the electrical and control systems should also be assessed to ensure that the PLC, HMI, and other automation systems are up to date and running smoothly. Faulty wiring or outdated software could cause system errors, leading to costly downtime or inefficiencies.
Equally important is the availability of parts. A critical aspect of minimizing machine downtime is having quick access to replacement components. Machines like the steel wire drawing machine, which rely heavily on high-performance mechanical systems, require specific parts such as capstans, bearings, and motors, all of which wear out over time. Having a reliable parts supplier and maintaining an in-house inventory of commonly replaced parts can dramatically reduce wait times for repairs. It's also beneficial to establish a relationship with your machine manufacturer or supplier to ensure you can easily source original or high-quality compatible parts.
Some machines may also offer the option for customizable maintenance packages, which can help streamline the process and ensure you receive genuine parts and professional servicing when needed. Additionally, many manufacturers offer extended warranties that cover parts and labor for a certain period, further reducing the financial risk of unexpected breakdowns. Investing in these packages can provide peace of mind and allow businesses to focus more on production rather than machine maintenance.
The key to ensuring optimal performance for a steel wire drawing machine lies in maintaining a consistent and well-organized maintenance schedule. Regularly checking and replacing components before they fail will help avoid costly downtime and extend the life of the machine. Furthermore, securing easy access to high-quality replacement parts ensures that repairs can be made quickly and efficiently, keeping your production line running smoothly and maximizing your investment. Taking these steps can make all the difference between a machine that performs reliably for years and one that incurs frequent and expensive repairs.
Contact Us