Drawing wire to such small sizes demands more than just a powerful machine—it requires meticulous control over every part of the process. The accuracy of wire diameter at such small scales is influenced by a combination of high-quality equipment, skilled operation, and optimized techniques.
A key component in achieving this precision is the capstan, which plays a pivotal role in controlling the tension and speed of the wire during the drawing process. In machines designed to handle wire sizes as small as 0.03mm, the capstan needs to be of exceptional quality and highly durable, as it’s responsible for maintaining the necessary tension and drawing speed. High-quality capstans can ensure that even at these tiny diameters, the wire is drawn smoothly without variation, which is crucial for maintaining consistency.
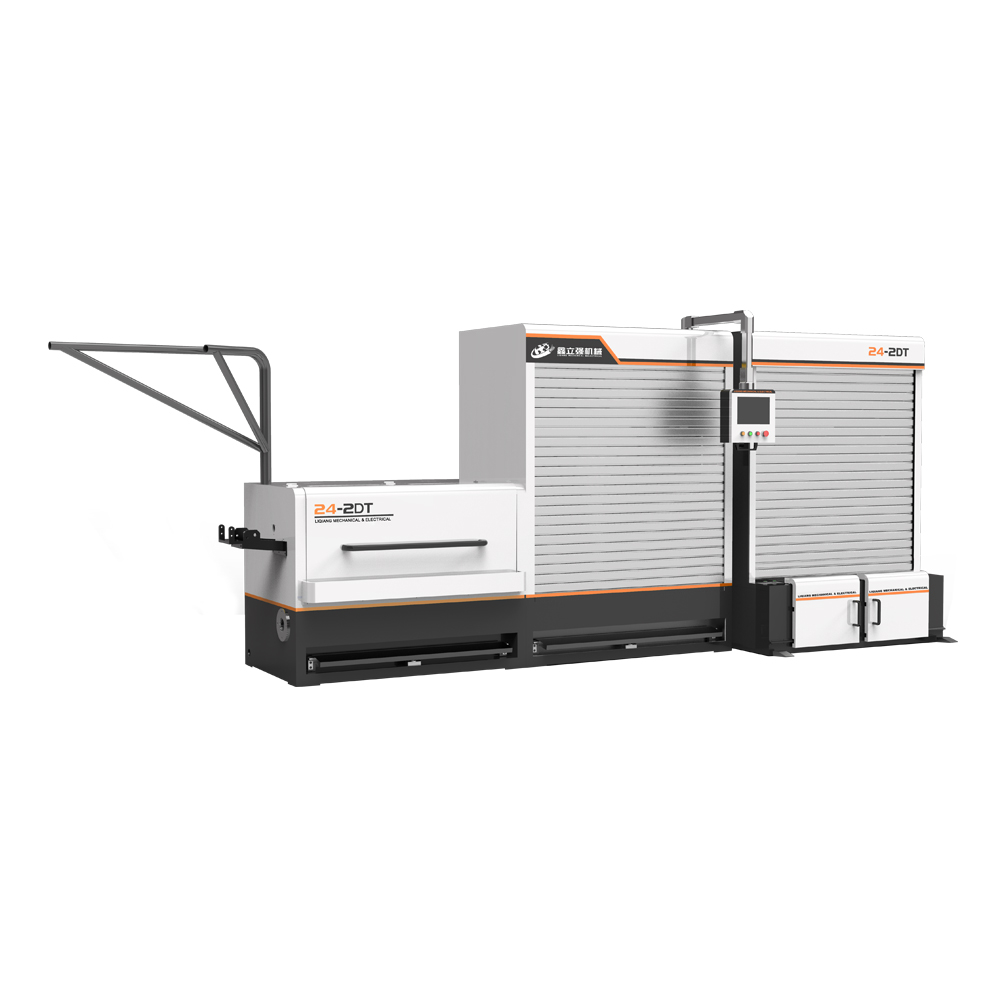
Another crucial element in achieving precise diameter control is the integration of advanced PLC and HMI systems. These systems allow for real-time monitoring and adjustments to ensure that the drawing speed, tension, and pressure are optimized at all stages. With such fine wires, even the smallest fluctuations in these parameters can cause variations in diameter, leading to inconsistencies that can affect product quality. The PLC system’s ability to provide instant feedback and adjust settings on the fly helps eliminate these risks, making sure the wire maintains its intended diameter with minimal deviation.
However, the importance of the rapid die-change system should not be overlooked, especially when working with very fine diameters. The ability to quickly swap out dies without significant downtime is not just about convenience—it’s about ensuring that the drawing process remains consistent and efficient, especially when switching between different wire sizes. A high-quality die-change system allows for smoother transitions and better control, which is crucial when you're working with precision targets like 0.03mm.
Moreover, the overall maintenance of the machine plays a significant role in sustaining consistent wire quality over time. Machines that are regularly serviced and maintained ensure that all components, especially those involved in the drawing process, continue to function optimally. Regular maintenance checks on the capstan, dies, and tension control systems can prevent even small issues from becoming larger problems that might impact the wire diameter accuracy. It’s also worth noting that modern copper wire drawing machines are often built to be more energy-efficient, which not only reduces operational costs but also keeps the process stable, preventing power surges that could disrupt the fine-tuning required for such tiny wire sizes.
Achieving precision in drawing copper wire to 0.03mm is about a lot more than just the machine’s technical specifications. It’s about integrating the right technologies, ensuring proper maintenance, and understanding how every part of the machine interacts with each other to deliver a flawless end product. When all these elements align, customers can be confident that their wire will meet the stringent requirements of their specific applications, whether they’re used in delicate electronics, telecommunications, or other specialized fields.
Contact Us