Belt transmission systems, in particular, have gained attention for their practicality and ease of maintenance. But how do they compare to more traditional gear and chain systems, especially when it comes to long-term efficiency and upkeep? This is an important question because it influences not only the cost of maintenance but also the overall performance and productivity of the machine.
Belt-driven systems, commonly found in modern Brass Wire Drawing Machines, are celebrated for their simplicity and reliability. These systems use flexible belts, often made of materials like rubber or synthetic composites, to transfer power from one part of the machine to another. One of the primary advantages of a belt system is its low maintenance requirement. Unlike gears or chains, which often require frequent lubrication, adjustments, and replacements due to wear and tear, belt transmission systems are relatively low-maintenance. Belts typically do not require any lubrication, which significantly reduces downtime for maintenance tasks. They are also easier to replace and adjust when necessary, offering a cost-effective solution for ongoing machine operation.
In terms of efficiency, belts generally provide smooth and quiet operation, which is an advantage in reducing noise pollution in a production environment. They are also capable of handling a range of speeds and can be easily adjusted for varying workloads, making them versatile for different wire drawing applications. This flexibility enhances the efficiency of the overall production process by accommodating different wire sizes and materials. Moreover, the continuous, even force distribution provided by belts helps in achieving consistent wire drawing without the risk of jerks or fluctuations that can sometimes occur with chain or gear-driven machines.
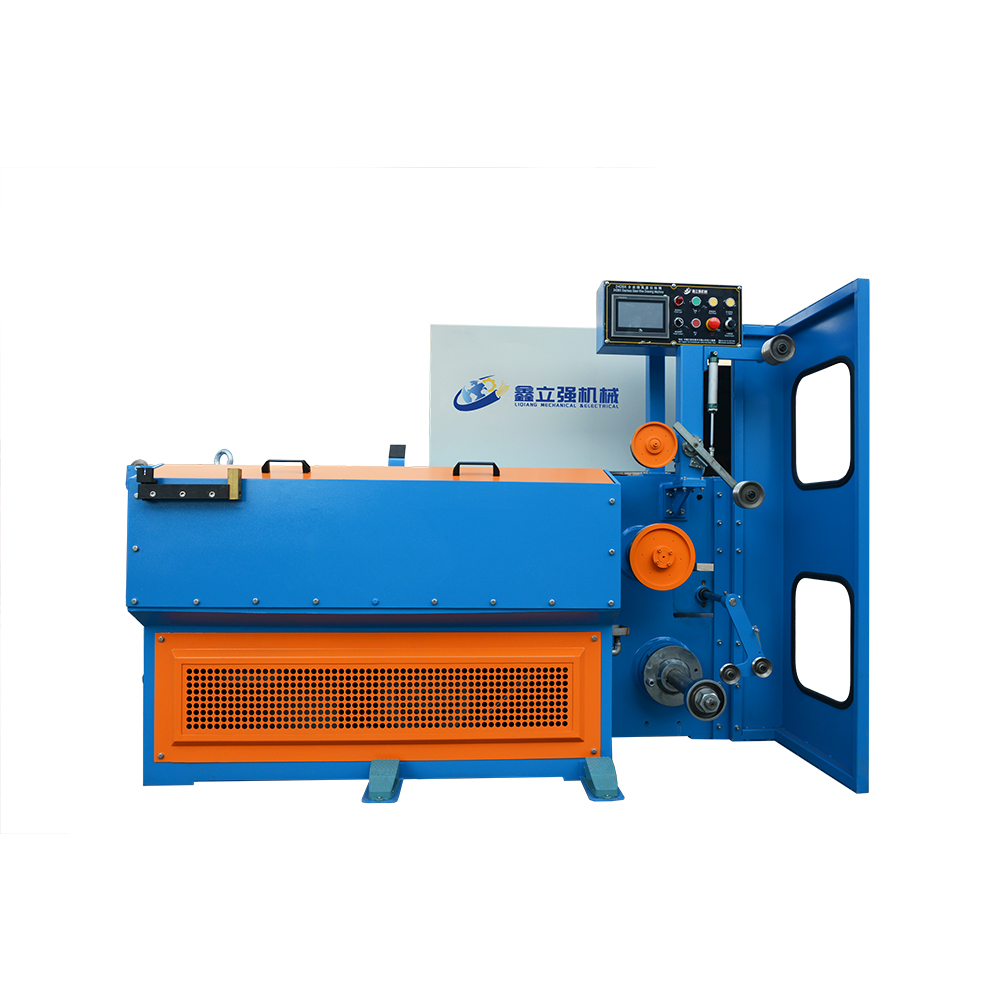
However, while belt transmission systems offer several benefits, there are situations where gear or chain systems might be preferred. Gear-driven systems, for instance, are known for their ability to handle high loads with exceptional precision. They are often used in heavy-duty applications where maximum torque and power transmission are essential. Chains, like gears, are ideal for transmitting power over longer distances or in applications that demand heavy load handling. However, both systems require more frequent maintenance than belts. Chains, for example, must be regularly lubricated to prevent wear, while gears need to be checked for alignment and tooth condition to ensure efficient power transfer.
When it comes to efficiency, belt systems excel in most wire drawing applications because of their ability to run quietly and smoothly, which is crucial in reducing noise and vibrations in the factory. Chains and gears, on the other hand, can produce more noise and require more energy to maintain the same level of operation. They also tend to create more friction, which can decrease overall energy efficiency. Furthermore, while gears and chains may offer higher torque capacity, the flexibility and ease of adjustment offered by belt systems often outweigh this advantage, especially for machines used in industries like brass wire drawing, where moderate to high power is sufficient.
The choice between a belt, gear, or chain transmission system will depend on the specific needs of the production line. If ease of maintenance and lower operational costs are a priority, a belt-driven system is likely the better choice. It offers the efficiency and versatility required for drawing brass wire, without the constant upkeep associated with gears or chains. For companies looking to minimize downtime and maintenance costs, the belt transmission system stands out as an excellent option, delivering reliable and smooth operation for the long term.
Contact Us