Brass wire drawing machines are indispensable tools in wire production, especially when manufacturing precision brass wires for applications like electrical discharge machining (EDM). One of the key features of these machines is their ability to work with a wide range of drawing dies to produce brass wire in various sizes. The performance of the machine and the flexibility it offers largely depends on how well it handles die changes and how many different die options are available. The die selection and changeover process can greatly affect the efficiency, quality, and operational costs of the entire wire drawing setup, making it an essential consideration for businesses looking to optimize production.
Brass wire drawing machines typically support an extensive range of dies designed for different wire diameters and properties. The dies, which are crucial for shaping the brass wire to precise dimensions, are made of high-quality materials like tungsten carbide, which can withstand the intense pressures and abrasion during the drawing process. The ability to use various dies allows the machine to produce wire with diameters ranging from a few millimeters down to very fine gauges, depending on the application. Whether you're working with thicker brass wires for industrial use or fine wires for delicate operations like EDM, the machine can adapt to different die sizes to meet the demands of production. The versatility in die selection is especially important for industries that require varying wire thicknesses for different products, such as electronics, automotive components, or even jewelry making.
Changing the dies on a brass wire drawing machine is a crucial aspect of the overall production process. The ease with which these dies can be changed directly impacts productivity, maintenance costs, and the overall efficiency of the manufacturing operation. In traditional wire drawing machines, changing dies can be a time-consuming process that requires skilled labor and careful handling to ensure that the machine is not damaged during die installation or removal. However, modern brass wire drawing machines have evolved to make this process as efficient and straightforward as possible. Many machines feature quick-change die mechanisms, allowing operators to swap out dies with minimal downtime. This means that businesses can quickly shift from one wire diameter to another without the need for extensive re-calibration, which helps in maintaining high throughput and reducing production delays.
Moreover, the use of advanced technology like Siemens PLC and HMI systems further streamlines the die change process. These systems provide real-time data on the machine’s performance and help operators make adjustments or troubleshoot issues related to the drawing process. When a die change is required, the system can guide the operator through the procedure, ensuring that the new die is installed correctly and that the machine is set to the right parameters for the new wire size. This integration of automation not only simplifies the die-changing procedure but also minimizes the risk of errors that could lead to defective products or machine malfunction.
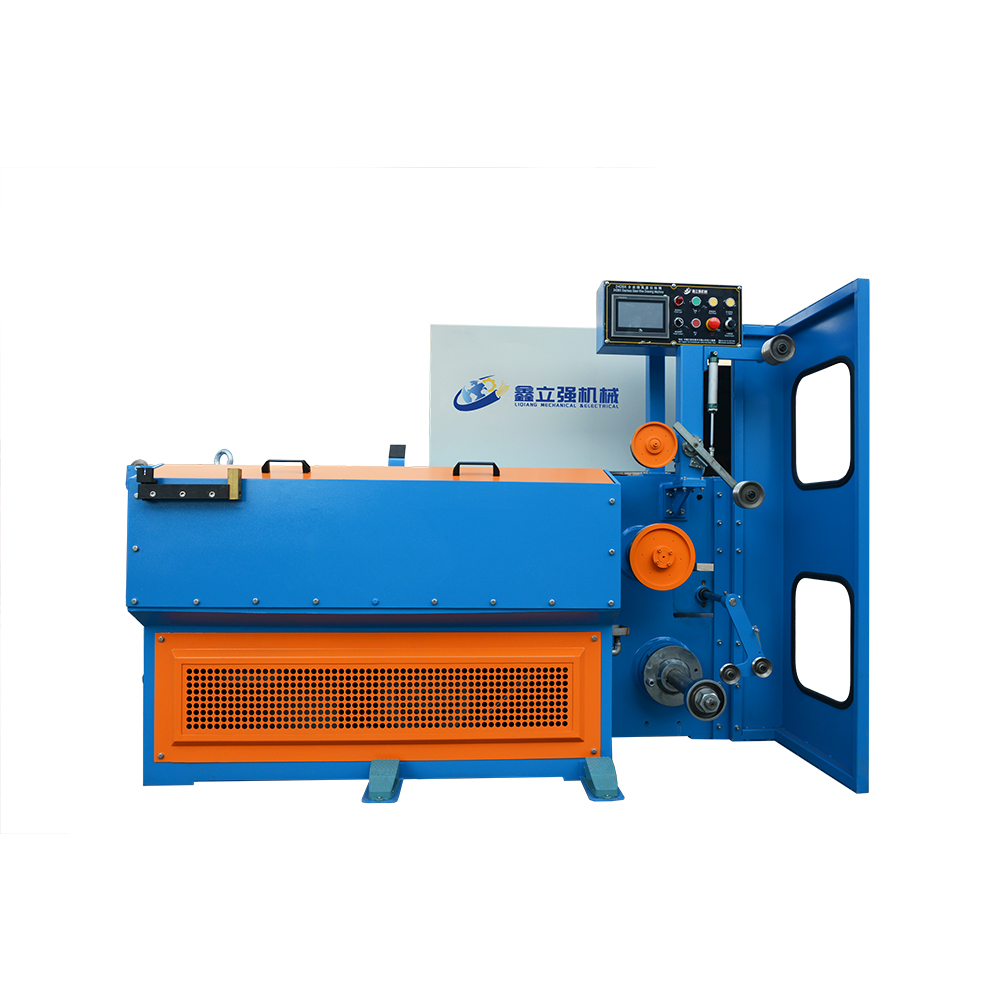
While the ease of die change is important, it’s also essential to consider the range of dies that a Brass wire drawing machines can support. A machine with a wider range of compatible dies provides greater flexibility, allowing manufacturers to produce different types of wire without needing to invest in multiple machines. This flexibility is particularly valuable for businesses that produce custom orders or need to adapt quickly to market demands. Some machines are equipped with automatic tension control systems, which also play a role in ensuring that the wire is drawn evenly across all sizes, further improving the overall quality and consistency of the wire produced.
In addition to the mechanical aspects of die changing, businesses also need to consider the longevity and quality of the dies themselves. Tungsten carbide dies, for example, are known for their durability and resistance to wear, which reduces the frequency of replacements and helps keep operational costs down. However, maintaining a stock of spare dies and ensuring that they are regularly inspected for signs of wear is still an essential part of managing a wire drawing operation. With the right maintenance schedule, companies can ensure that their brass wire drawing machines continue to perform at their best, producing high-quality wire efficiently and with minimal disruption.
Contact Us