Types of Lubricants Used
Brass wire drawing machines rely on specialized lubricants tailored for metal drawing processes. These lubricants are formulated to reduce friction between the brass wire and the drawing dies, thereby minimizing wear and heat generation during the drawing process. The selection of lubricants is critical, as they directly influence the quality of the drawn wire and the operational efficiency of the machine.
Application Methods
The application of lubricants is carefully managed to maintain operational integrity and maximize efficiency:
Immersion Method: In this method, the brass wire passes through a bath of lubricant before entering the drawing die. This ensures consistent coating of lubricant on the wire surface, reducing friction as it progresses through the drawing stages.
Spraying Method: Alternatively, lubricants can be sprayed directly onto the brass wire just before it enters the drawing die. This method allows for precise control over the amount of lubricant applied, adjusting to the specific requirements of different wire sizes and drawing speeds.
Die Coating: Some drawing dies are designed with integrated lubricant reservoirs or coatings. These reservoirs continuously apply a controlled amount of lubricant onto the wire surface as it passes through the die, ensuring uniform lubrication throughout the drawing process.
Monitoring and Control
Maintaining optimal lubrication levels is crucial for consistent performance:
Automated Systems: Modern brass wire drawing machines often feature automated lubrication systems. These systems utilize sensors and feedback mechanisms to monitor parameters such as wire speed, tension, and temperature. Based on these inputs, the system adjusts lubricant flow rates to ensure optimal performance and minimal waste.
Manual Adjustment: In some cases, operators may manually adjust lubricant application settings based on production requirements and visual inspections of the wire quality. This hands-on approach ensures flexibility and responsiveness to changing conditions during operation.
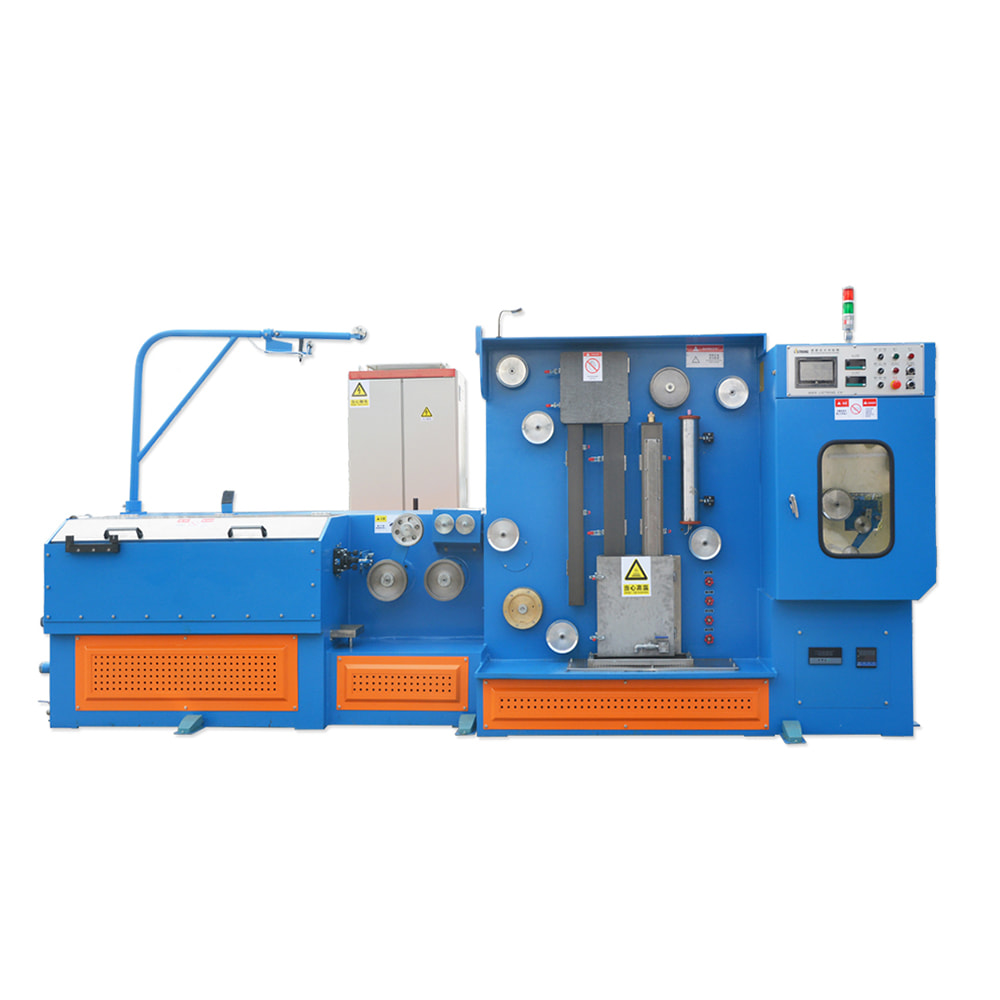
Maintenance Practices
To uphold smooth operations and prolong equipment life, regular maintenance of the lubrication system is essential:
Cleaning and Refilling: Lubricant reservoirs and application devices require periodic cleaning and refilling to prevent contamination and ensure consistent lubricant quality.
Inspections: Routine inspections of lubricant delivery mechanisms, such as spray nozzles or immersion baths, help identify and rectify any issues promptly. This proactive approach minimizes downtime and maintains production efficiency.
Quality Control: Quality control measures include monitoring lubricant viscosity, cleanliness, and chemical composition to uphold performance standards and adhere to environmental regulations.
Performance Benefits
Efficient lubrication management offers several benefits that contribute to overall operational excellence:
Reduced Friction: Properly lubricated brass wire experiences reduced friction as it passes through drawing dies, minimizing heat generation and preserving wire integrity.
Enhanced Efficiency: Smooth operations translate to higher throughput and consistent wire quality, meeting stringent manufacturing specifications.
Extended Equipment Life: Effective lubrication mitigates wear and tear on drawing dies and other critical components, extending the lifespan of the machine and reducing maintenance costs over time.
Environmental Considerations
In the pursuit of sustainable manufacturing practices, Brass wire drawing machines consider environmental implications:
Eco-Friendly Lubricants: Where feasible, using environmentally friendly lubricants helps minimize ecological footprint and complies with regulatory standards for waste disposal.
Efficient Resource Utilization: Optimizing lubricant usage reduces material waste and energy consumption, aligning with corporate sustainability goals.
Contact Us