In the bustling world of wire and cable manufacturing, efficiency and reliability are paramount. At the heart of this industry lies the wire cable bunching machine, a critical piece of equipment tasked with twisting multi-strand bare copper and tinned wires to create the intricate cables that power our modern world. However, like any mechanical system, these machines require periodic maintenance and occasional part replacement to ensure smooth operations. The question then arises: How easy is it to access and replace worn or damaged parts in wire cable bunching machines?
The answer lies in the intricate interplay of design, engineering, and user experience.
Accessible Components:
One of the key factors influencing the ease of maintenance is the accessibility of machine components. Manufacturers understand the importance of quick access to vital parts for maintenance and repair. Thus, many wire cable bunching machines are designed with easily removable panels or covers, allowing operators to swiftly reach the components that require attention. Whether it's the twisting mechanism or the motor assembly, accessibility is prioritized to minimize downtime and maximize productivity.
Clear Documentation:
Navigating the inner workings of a wire cable bunching machine can be daunting without proper guidance. To alleviate this concern, manufacturers provide comprehensive documentation, including manuals, schematics, and parts lists. These resources serve as indispensable guides, empowering operators to confidently undertake maintenance tasks and replace worn or damaged parts with precision and efficiency.
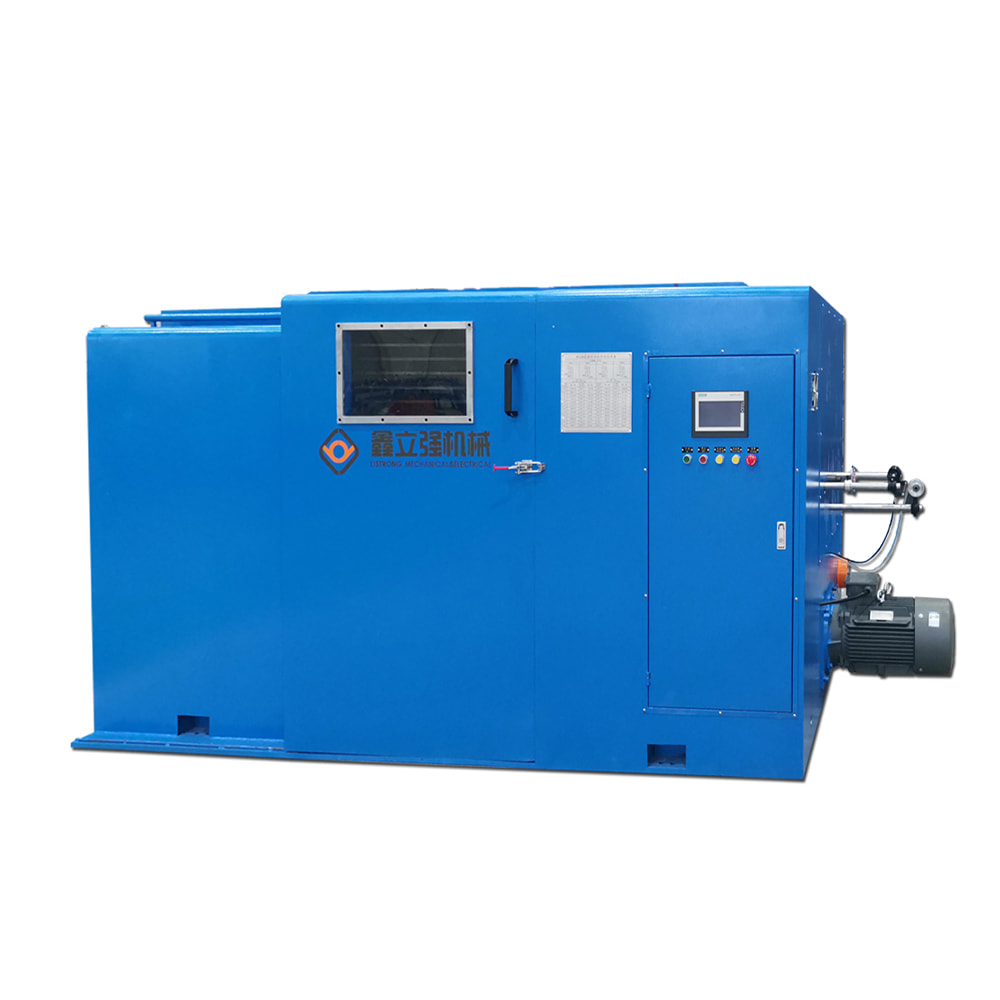
Standardized Parts:
In the world of machinery, compatibility is king. Wire cable bunching machines that utilize standardized or widely available parts for common components simplify the replacement process. Operators can easily source compatible replacements, reducing the time spent searching for elusive components and minimizing disruption to production schedules.
Modular Design:
Modularity is a hallmark of modern machinery design, and wire cable bunching machines are no exception. By organizing components into interchangeable modules, manufacturers facilitate maintenance and repair procedures. In the event of a malfunction or part failure, operators can swiftly swap out entire modules, streamlining the replacement process and minimizing downtime.
Training and Support:
Knowledge is power, especially when it comes to machine maintenance. Recognizing this, manufacturers offer comprehensive training programs and support services to equip operators with the skills and knowledge necessary to maintain and repair wire cable bunching machines effectively. Armed with this expertise, operators can tackle maintenance tasks with confidence, ensuring uninterrupted operations.
Supplier Support:
In the event of complex repairs or specialized part requirements, manufacturers maintain extensive networks of suppliers and service centers. These resources serve as invaluable lifelines, providing operators with access to expert assistance and genuine replacement parts. Whether it's troubleshooting a technical issue or sourcing a critical component, supplier support ensures that operators can overcome any challenge with ease.
In conclusion, the ease of accessing and replacing worn or damaged parts in wire cable bunching machine is a testament to the synergy of design innovation and user-centricity. From accessible components and clear documentation to standardized parts and modular design, manufacturers have engineered these machines with maintenance in mind. Coupled with comprehensive training and robust supplier support, operators are empowered to keep their wire cable bunching machines running smoothly, ensuring uninterrupted productivity in the dynamic world of wire and cable manufacturing.
Contact Us