The accuracy and consistency of wire diameter in a
wire making machine are crucial for ensuring the quality of the produced wires. Various mechanisms and control systems are employed to maintain precision throughout the production process.
Precision Dies: The wire making machine typically includes precision dies through which the wire passes during the manufacturing process. These dies are designed to shape and size the wire accurately. Regular inspection and maintenance of the dies are essential to prevent wear and ensure consistent wire diameter.
Automated Tension Control: Automated tension control systems are employed to regulate the tension of the wire during the manufacturing process. Consistent tension is crucial for maintaining uniform wire diameter. These systems can adjust tension levels based on the wire type, material, and production speed.
Closed-Loop Feedback Systems: Sophisticated wire making machines often use closed-loop feedback systems. Sensors and monitoring devices measure the actual wire diameter in real-time. This information is then fed back to the machine's control system, which can make instantaneous adjustments to maintain the desired diameter.
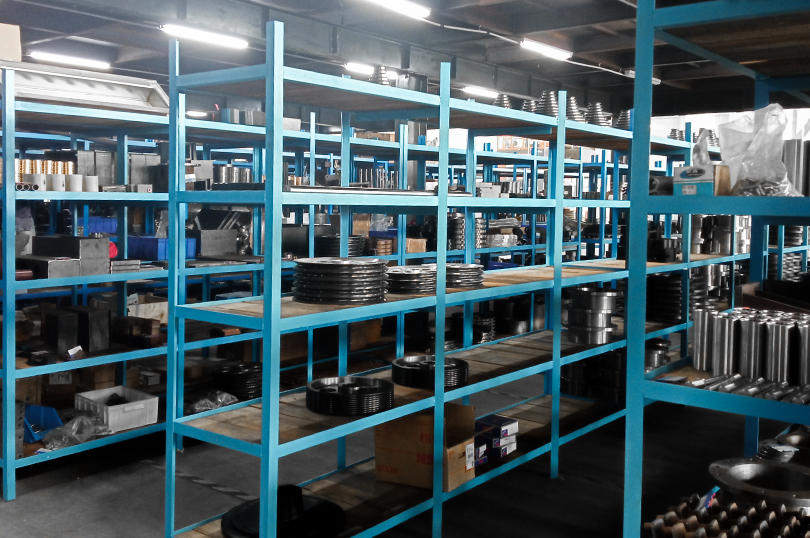
Diameter Measurement Devices: Inline diameter measurement devices, such as laser sensors or micrometers, can be integrated into the machine. These devices measure the diameter of the wire as it is being produced, and the data is used to make automatic adjustments to the manufacturing process.
Calibration Processes: Regular calibration of the machine is essential for ensuring accuracy. This involves checking and adjusting the machine's components, including dies, sensors, and measuring devices, to maintain their accuracy over time.
Quality Control Inspections: Quality control inspections are conducted at various stages of the production process. Random samples of the produced wire are measured and inspected to verify that they meet the specified diameter tolerances. Any deviations can trigger adjustments to the machine settings.
Material Quality Control: The quality of the raw materials, such as the metal or alloy used in wire production, is critical. Strict quality control measures for incoming materials help ensure consistency in wire diameter.
Machine Calibration based on Material Characteristics: Different materials may have unique characteristics that affect their behavior during the manufacturing process. The
wire making machine may have settings that can be calibrated based on the specific material being used to optimize diameter consistency.
Temperature Control: Some materials may exhibit variations in diameter based on temperature. Temperature control systems can be implemented to stabilize the production environment and minimize temperature-related fluctuations in wire diameter.
Contact Us