In the world of wire drawing, small technical details often make a big difference—and one such detail is the slip ratio. For those working with Aluminum Wire Rod Breakdown Machines, understanding slip is not just a matter of technical curiosity but a real factor that influences the consistency and quality of the final product. Slip occurs when there’s a mismatch between the surface speed of the drawing capstan and the speed at which the wire moves through the die. A high slip ratio can cause surface defects, heat build-up, and uneven elongation, especially in continuous, high-speed production environments where stability and repeatability are key.
When a machine is designed to operate with a small or minimal slip ratio, as is the case with modern horizontal-type aluminum rod breakdown machines, the advantages are clear. Reduced slip means the wire is subjected to more consistent tension throughout the drawing process, which leads to better surface smoothness and dimensional accuracy. This is particularly important when drawing aluminum, which is more sensitive to deformation and surface damage compared to harder metals like copper. Maintaining low slip not only ensures a more uniform wire but also contributes to the overall mechanical performance of the end product, which is vital in applications such as electrical transmission or structural cabling.
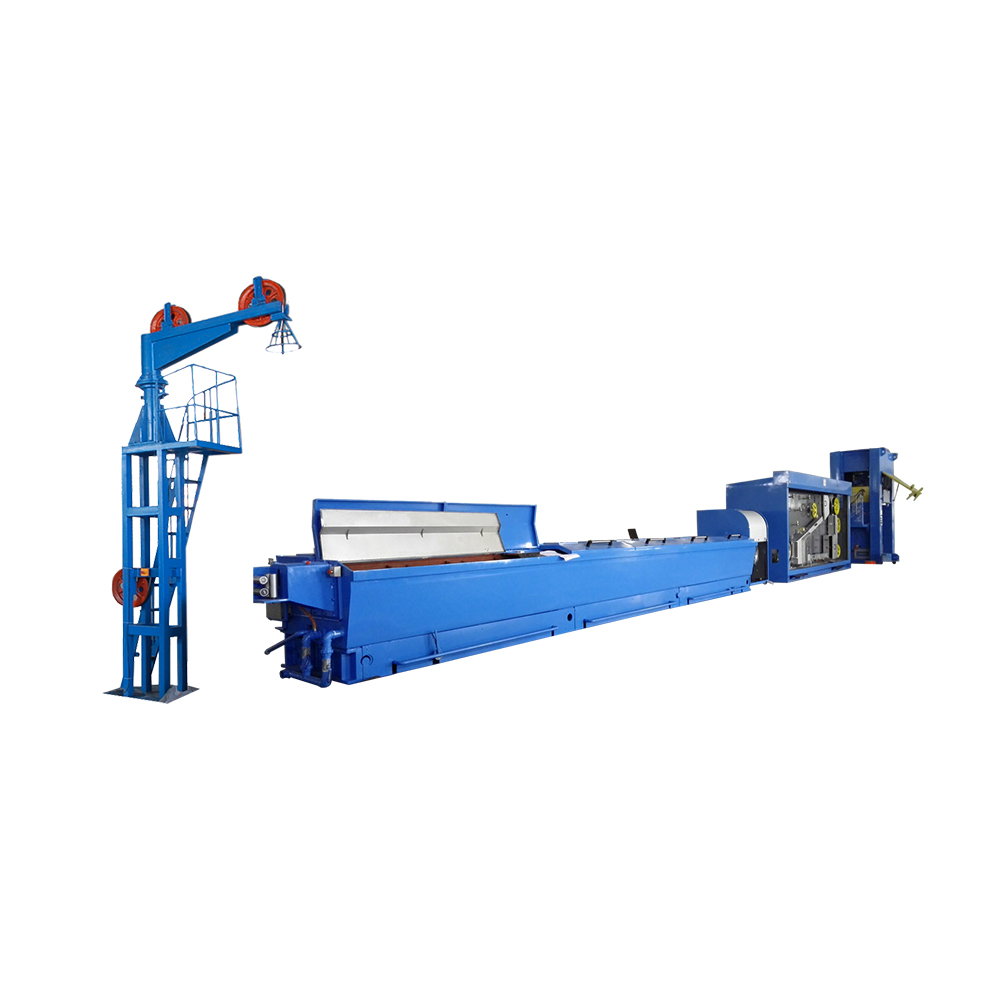
From a mechanical standpoint, achieving a small slip ratio requires precise synchronization between the motor, capstans, and die setup. That’s where machine design becomes critical. Well-engineered aluminum rod breakdown machines incorporate precision gear ratios and intelligent control systems to ensure that the drawing process remains stable even under varying loads. These systems are fine-tuned through experience, especially in manufacturing environments where consistency isn’t just a preference—it’s a production standard. That’s why experienced manufacturers invest heavily in refining the mechanical harmony of their equipment to keep slip levels tightly controlled.
Moreover, keeping slip low doesn't only benefit the wire—it benefits the machine itself. High slip increases friction and wear on both the wire and the dies, which leads to more frequent maintenance stops and higher operating costs. A low-slip design reduces thermal stress and prolongs the life of the consumable parts, offering a practical and cost-effective advantage for wire manufacturers. In today’s competitive landscape, where operational efficiency and product quality go hand in hand, having a wire drawing machine that minimizes slip becomes a strategic asset.
In fact, this is one of the reasons customers choose our Aluminum Wire Rod Breakdown Machines—not just for their high efficiency and clean finish, but for the way they're engineered to control critical variables like slip. For clients seeking a balance of durability, precision, and performance, this kind of design focus translates directly into long-term value. We’ve seen time and again how even small improvements in drawing stability can deliver big returns in terms of product consistency and downstream processing success.
In the end, while slip ratio might not be the first spec that jumps out on a datasheet, it’s one of those behind-the-scenes features that separates average machines from truly professional solutions. For manufacturers serious about wire quality and long-term production reliability, paying attention to slip—and choosing a machine designed to minimize it—is a smart move. Whether you're upgrading your existing line or expanding capacity, understanding the mechanics behind aluminum rod breakdown machines helps you make more informed, future-proof decisions.
Contact Us