At its core, the automatic correction control system utilizes advanced sensors and algorithms to monitor the tension of the wire as it is drawn. These sensors continuously gather data on the wire’s tension levels, providing real-time feedback to the control system. If the tension deviates from the predetermined setpoint—whether due to fluctuations in material properties or variations in drawing speed—the system automatically adjusts the parameters to bring the tension back into the optimal range. This dynamic adjustment is not just reactive; it’s proactive, ensuring that the machine operates smoothly without the need for constant manual intervention. The result is a consistent tension throughout the drawing process, which is essential for producing wire that meets strict industry standards.
The benefits of maintaining precise coiling tension through this automated system are substantial. For one, it significantly reduces the likelihood of defects such as kinks or uneven diameters, which can occur if the tension is not managed properly. A wire with inconsistent tension can lead to costly production delays and increased scrap rates. Moreover, the automatic system enhances the overall efficiency of the production line. By ensuring that the drawing process runs smoothly, operators can focus on other critical aspects of production rather than constantly monitoring tension levels. This not only saves time but also optimizes labor resources, leading to higher productivity and profitability.
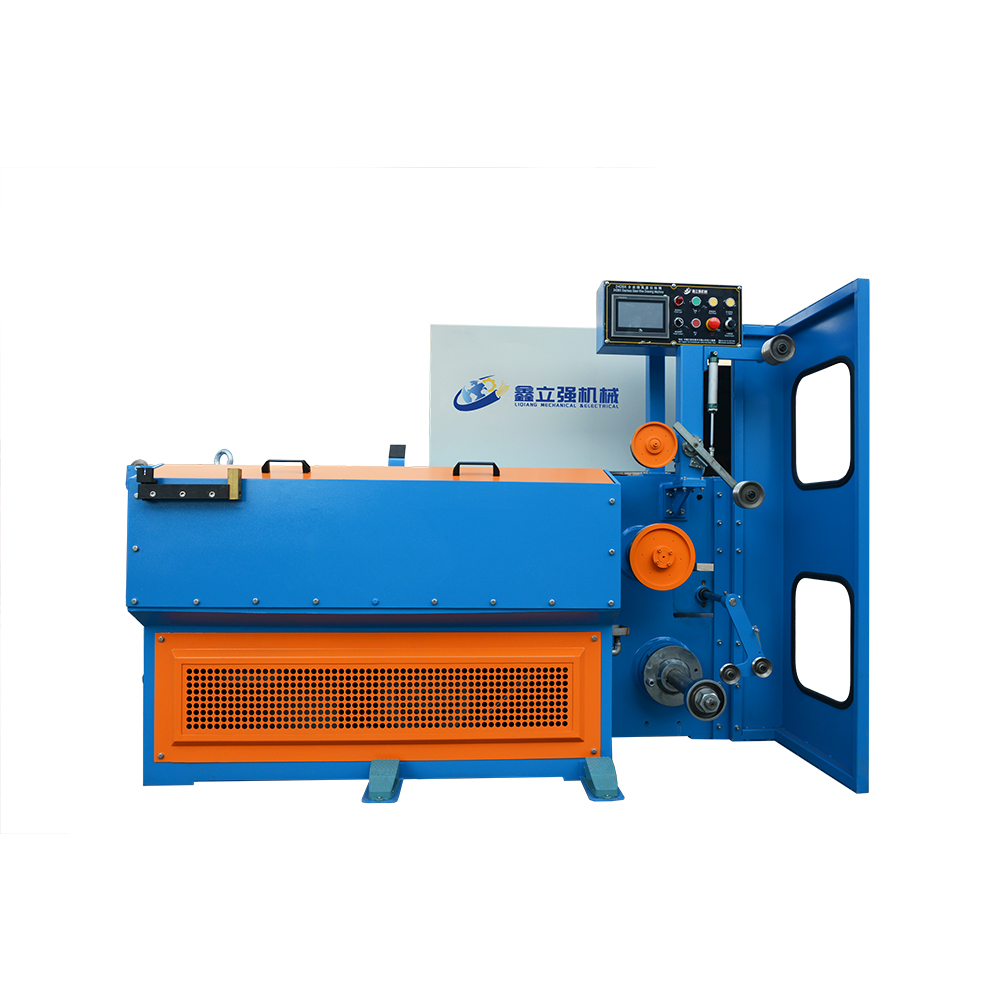
Another notable advantage is the enhanced safety that comes from automated tension management. Traditional systems often rely on manual adjustments, which can be hazardous, especially in high-speed operations. With the automatic correction control system in place, operators can work with greater peace of mind, knowing that the system is actively monitoring and adjusting tension as needed. This reduces the risk of accidents related to equipment failure or operator error, creating a safer work environment.
The automatic correction control system is a game-changer in the realm of brass wire drawing machines. By ensuring optimal coiling tension through real-time monitoring and adjustments, it not only enhances the quality and consistency of the wire produced but also streamlines operations, improves safety, and boosts overall efficiency. As industries continue to demand higher quality and more efficient production methods, technologies like this will undoubtedly play a pivotal role in shaping the future of wire manufacturing.
Contact Us